Precision CNC Turning Milling Parts for Industrial Applications
By:Admin
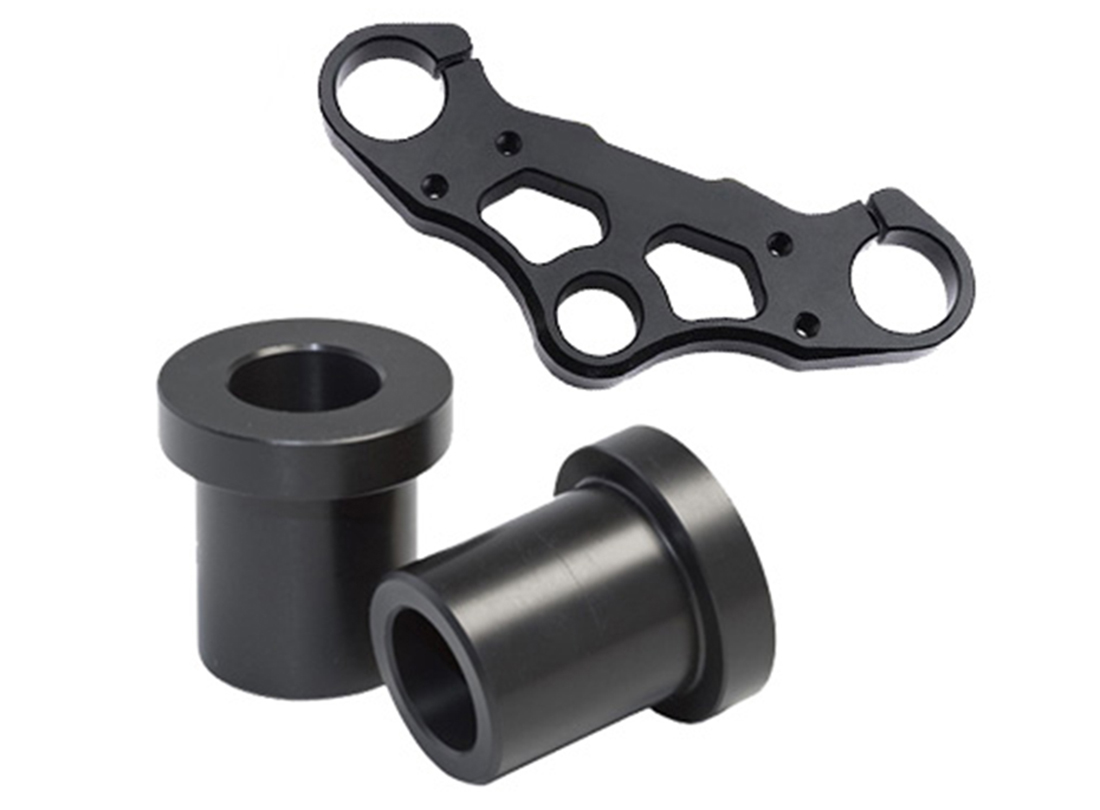
[Company Name] has established itself as a reliable and innovative supplier of precision machining solutions for a wide range of industries, including aerospace, automotive, medical, and more. With an unwavering commitment to quality and customer satisfaction, the company has earned a stellar reputation in the industry.
The CNC turning milling parts offered by [Company Name] are manufactured using state-of-the-art equipment and cutting-edge techniques. This allows for the production of highly complex and intricate components with tight tolerances and superior surface finishes. Whether it's a small batch of custom parts or large-scale production runs, the company has the capability to meet the diverse needs of its clients with precision and efficiency.
One of the key advantages of CNC turning and milling is the ability to produce parts with a high degree of accuracy and consistency. This is especially crucial for industries that demand strict adherence to specifications and standards, such as aerospace and medical. [Company Name] understands the critical nature of these requirements and has invested in the latest CNC technology to ensure that its parts consistently meet the highest quality standards.
In addition to its state-of-the-art manufacturing capabilities, [Company Name] prides itself on its team of highly skilled engineers, machinists, and quality control professionals. These experts work closely with clients from the initial design phase through to the final production, offering valuable insights and expertise to optimize the manufacturability and performance of the parts. This collaborative approach has enabled [Company Name] to develop long-lasting partnerships with its clients, built on trust, reliability, and superior results.
Furthermore, [Company Name] places a strong emphasis on continuous improvement and innovation. The company regularly invests in new technologies, training, and research to stay at the forefront of the industry. By doing so, it remains well-positioned to adapt to evolving market demands and deliver cutting-edge solutions to its clients.
With a commitment to sustainability and social responsibility, [Company Name] also focuses on environmentally friendly manufacturing practices and ethical business conduct. It prioritizes the use of energy-efficient processes, recyclable materials, and waste reduction initiatives, contributing to a more sustainable manufacturing ecosystem.
In conclusion, [Company Name] stands out as a leading provider of CNC turning milling parts, offering a winning combination of advanced technology, expertise, and customer-centric values. As industries continue to evolve and demand higher precision and efficiency, the company is well-equipped to meet these challenges head-on, delivering top-quality solutions to its clients globally. With an unwavering dedication to excellence and innovation, [Company Name] is poised for even greater success in the years to come.
In conclusion, [Company Name] is a leading provider of CNC turning milling parts, offering a winning combination of advanced technology, expertise, and customer-centric values. As industries continue to evolve and demand higher precision and efficiency, the company is well-equipped to meet these challenges head-on, delivering top-quality solutions to its clients globally. With an unwavering dedication to excellence and innovation, [Company Name] is poised for even greater success in the years to come.
Company News & Blog
Precision CNC Turning Milling Parts for Industrial Applications
Over the past decade, the manufacturing industry has experienced a significant shift towards advanced technologies such as CNC turning and milling. These precision machining processes have revolutionized the production of various parts and components, offering increased efficiency, accuracy, and cost-effectiveness. One company at the forefront of this technological advancement is [Company Name], a leading provider of CNC turning milling parts.[Company Name] has established itself as a reliable and innovative supplier of precision machining solutions for a wide range of industries, including aerospace, automotive, medical, and more. With an unwavering commitment to quality and customer satisfaction, the company has earned a stellar reputation in the industry.The CNC turning milling parts offered by [Company Name] are manufactured using state-of-the-art equipment and cutting-edge techniques. This allows for the production of highly complex and intricate components with tight tolerances and superior surface finishes. Whether it's a small batch of custom parts or large-scale production runs, the company has the capability to meet the diverse needs of its clients with precision and efficiency.One of the key advantages of CNC turning and milling is the ability to produce parts with a high degree of accuracy and consistency. This is especially crucial for industries that demand strict adherence to specifications and standards, such as aerospace and medical. [Company Name] understands the critical nature of these requirements and has invested in the latest CNC technology to ensure that its parts consistently meet the highest quality standards.In addition to its state-of-the-art manufacturing capabilities, [Company Name] prides itself on its team of highly skilled engineers, machinists, and quality control professionals. These experts work closely with clients from the initial design phase through to the final production, offering valuable insights and expertise to optimize the manufacturability and performance of the parts. This collaborative approach has enabled [Company Name] to develop long-lasting partnerships with its clients, built on trust, reliability, and superior results.Furthermore, [Company Name] places a strong emphasis on continuous improvement and innovation. The company regularly invests in new technologies, training, and research to stay at the forefront of the industry. By doing so, it remains well-positioned to adapt to evolving market demands and deliver cutting-edge solutions to its clients.With a commitment to sustainability and social responsibility, [Company Name] also focuses on environmentally friendly manufacturing practices and ethical business conduct. It prioritizes the use of energy-efficient processes, recyclable materials, and waste reduction initiatives, contributing to a more sustainable manufacturing ecosystem.In conclusion, [Company Name] stands out as a leading provider of CNC turning milling parts, offering a winning combination of advanced technology, expertise, and customer-centric values. As industries continue to evolve and demand higher precision and efficiency, the company is well-equipped to meet these challenges head-on, delivering top-quality solutions to its clients globally. With an unwavering dedication to excellence and innovation, [Company Name] is poised for even greater success in the years to come.In conclusion, [Company Name] is a leading provider of CNC turning milling parts, offering a winning combination of advanced technology, expertise, and customer-centric values. As industries continue to evolve and demand higher precision and efficiency, the company is well-equipped to meet these challenges head-on, delivering top-quality solutions to its clients globally. With an unwavering dedication to excellence and innovation, [Company Name] is poised for even greater success in the years to come.
Unlocking the Potential of Insert Moulding: Explore its Benefits and Applications
[News Headline]Innovative Insert Moulding Technology Enhances Efficiency and Durability in Manufacturing Processes[Subheading]Leading Manufacturing Company Unveils Remarkable Insert Moulding Technique That Revolutionizes the Industry[City, Date] - In a bid to revolutionize manufacturing processes, a renowned manufacturing company introduces an innovative insert moulding technology that enhances efficiency, durability, and cost-effectiveness. This groundbreaking technique aims to address long-standing challenges faced by various industries and is set to provide a significant boost to the manufacturing sector.[City, Date] - With the rapid advancement of technology, manufacturers strive to stay ahead of the curve by implementing cutting-edge techniques and technologies. With the rise in customer demand for improved efficiency, increased durability, and cost-effectiveness, companies such as [Company Name] have answered the call with their groundbreaking insert moulding technology.Insert moulding, also known as overmoulding, is a highly specialized manufacturing process that involves injecting a pre-formed component, such as metal, plastic, or electronic parts, into a plastic mould. This innovative technique provides multiple advantages over traditional manufacturing methods, making it an attractive option for a wide range of industries.One significant advantage of insert moulding is the enhanced durability it offers. The process ensures that the inserted component is securely encased within the plastic material, providing added protection from external forces, reducing the risk of damage and increasing the lifespan of the final product. This durability is particularly beneficial in industries that require high-performance components, such as the automotive, aerospace, and electronics sectors.Moreover, insert moulding significantly streamlines the manufacturing process. By combining multiple manufacturing steps into one, companies can save time and resources, ultimately reducing production costs. This streamlined approach also reduces the potential for errors and inconsistencies commonly associated with manual assembly, ensuring a more precise and uniform final product.With the advent of insert moulding, manufacturers can also explore more intricate and complex designs. This technique allows for the creation of parts with intricate geometries and multiple materials, expanding the possibilities for innovative product design. Additionally, insert moulding enables designers to incorporate multiple functionalities into a single component, further enhancing efficiency and overall product performance.Speaking at a recent press conference, [Company Name]'s spokesperson highlighted the benefits of their insert moulding technology. "As a leader in the manufacturing industry, we continually strive to push the boundaries of innovation. Our insert moulding technique offers unparalleled advantages, ranging from increased durability and efficiency to expanded design possibilities. We are excited to provide our clients with this cutting-edge solution that can unlock significant improvements in their manufacturing processes."The introduction of insert moulding into the manufacturing industry marks a pivotal stage in the evolution of production techniques. With the increasing demand for efficient, durable, and cost-effective products, companies must adapt and embrace innovative technologies such as insert moulding to remain competitive.As various industries adopt this remarkable technology, it is expected to revolutionize production processes across the board. From automotive and aerospace to electronics and medical sectors, insert moulding will undoubtedly drive efficiency and durability to new heights, benefiting manufacturers and end-users alike.In a rapidly changing world, the introduction of insert moulding technology demonstrates the ability of companies like [Company Name] to continually innovate and provide solutions that meet the evolving needs of the manufacturing industry. As the demand for enhanced efficiency and durability continues to grow, insert moulding proves to be a game-changer for businesses aiming to stay ahead in a highly competitive market.
High-Quality Sheet Metal Bracket for Various Applications
Sheet Metal Bracket: A Breakthrough in Industrial ManufacturingAs technology continues to advance rapidly, industries are constantly seeking new and innovative ways to improve the efficiency and quality of their products. One such breakthrough that is revolutionizing the industrial manufacturing sector is the development of Sheet Metal Bracket.Sheet Metal Bracket, also known as [], is a cutting-edge solution that is proving to be a game-changer for companies involved in metal fabrication and manufacturing. This revolutionary technology has the potential to significantly improve the production process, reduce costs, and enhance the overall quality of the products being manufactured.With the help of Sheet Metal Bracket, companies can now produce highly complex and precise sheet metal components with an unprecedented level of accuracy. This is made possible by the use of advanced software and high-precision machinery that allows for intricate designs and shapes to be flawlessly cut and formed from sheet metal.In addition to its precision, Sheet Metal Bracket also offers remarkable flexibility, enabling manufacturers to efficiently produce a wide range of products, from simple brackets to intricate components for the automotive, aerospace, and electronics industries. This flexibility makes it a highly versatile and cost-effective solution for companies looking to streamline their production processes.Furthermore, the use of Sheet Metal Bracket has the potential to significantly reduce waste and material usage, as it allows for more efficient cutting and nesting of parts on the sheet metal. This not only contributes to cost savings but also aligns with the growing emphasis on sustainability and environmental responsibility in the manufacturing industry.One company at the forefront of this technological advancement is [], a leading manufacturer in the metal fabrication and manufacturing sector. With a focus on innovation and cutting-edge technology, [] has integrated Sheet Metal Bracket into its production processes, allowing the company to elevate the quality and precision of its products while maintaining cost-effectiveness.The adoption of Sheet Metal Bracket has enabled [] to expand its product offerings and cater to a wider range of industries and applications. With the ability to produce highly complex and intricate components, [] has positioned itself as a key player in the market, offering its customers unparalleled quality and precision in their metal fabrication needs.Moreover, the implementation of Sheet Metal Bracket has allowed [] to optimize its production processes, reducing lead times and enhancing overall efficiency. This has translated into improved customer satisfaction and a stronger competitive edge in the industry.As the demand for high-quality sheet metal components continues to grow across various industries, the adoption of Sheet Metal Bracket is expected to become increasingly prevalent. Its ability to deliver precise, complex, and cost-effective solutions makes it a valuable asset for manufacturers looking to stay ahead in a rapidly evolving market.In conclusion, the development of Sheet Metal Bracket represents a significant milestone in the field of industrial manufacturing. Its ability to deliver unparalleled precision, flexibility, and cost-effectiveness is reshaping the way companies approach metal fabrication and production. With forward-thinking companies like [] leading the way, the widespread adoption of Sheet Metal Bracket is set to revolutionize the industry and drive it towards a more efficient and sustainable future.
Unlocking Innovation: A Comprehensive Guide to Prototype Molds for Effective Product Development
Prototype Molds: Pioneering the Future of 3D Printing[City Name], [Date] - Prototype Molds, a leading player in the field of additive manufacturing and 3D printing, is revolutionizing the way products are designed and manufactured. With cutting-edge technology, a dedication to innovation, and a commitment to customer satisfaction, Prototype Molds is leading the way towards a future where 3D printing is the norm.Introduction:Prototype Molds, founded in [Year], has been at the forefront of additive manufacturing for over a decade. The company offers a wide range of services including rapid prototyping, 3D printing, and injection molding. With a team of skilled engineers, designers, and technicians, Prototype Molds has established itself as a go-to partner for companies looking to bring their ideas to life.Innovation in Additive Manufacturing:As one of the pioneers in the field of 3D printing, Prototype Molds has consistently pushed the boundaries of what is possible in manufacturing. Their state-of-the-art facility is equipped with the latest 3D printing technologies, allowing them to produce complex parts and prototypes with unparalleled precision. They have invested heavily in research and development, constantly striving to enhance the capabilities of their machines and processes.One major breakthrough by Prototype Molds is the development of high-performance materials for 3D printing. Through in-house research and partnerships with material suppliers, they have created a diverse range of materials that can meet the requirements of various industries, including aerospace, automotive, medical, and consumer electronics. These materials are not only durable and lightweight but also possess excellent mechanical properties, making them ideal for functional prototypes and end-use parts.Customer-Centric Approach:Prototype Molds understands the importance of customer satisfaction and collaboration. They work closely with clients from the initial design phase all the way through to the production of the final product. By involving clients at every step of the process, Prototype Molds ensures that their expectations are met, and the end result is a high-quality product that aligns with their vision.The company provides efficient and cost-effective solutions, allowing clients to bring their designs to market in a fraction of the time compared to traditional manufacturing methods. This significantly reduces development costs and gives companies a competitive edge in the fast-paced world of product innovation. Prototype Molds also offers expertise in design optimization, helping clients streamline their products for better performance and manufacturability.Continuous Growth and Expansion:Prototype Molds has experienced rapid growth and success in recent years, expanding its operations to serve a global clientele. The company's reputation for delivering exceptional quality and its commitment to innovation have attracted clients from a wide range of industries, including Fortune 500 companies and startups alike.To meet the increasing demand for its services, Prototype Molds has recently invested in expanding its production capabilities and adding new machines. This expansion allows them to handle larger projects, cater to more clients simultaneously, and maintain quick turnaround times without compromising on quality.Community Engagement and Environmental Responsibility:Prototype Molds recognizes the importance of giving back to the community and being environmentally responsible. The company actively engages in various initiatives to support local schools and educational institutions, fostering an interest in STEM education and empowering the next generation of innovators. Additionally, they have implemented sustainable practices in their manufacturing processes, reducing waste and minimizing their carbon footprint.Conclusion:Prototype Molds continues to push the boundaries of what is achievable in additive manufacturing, revolutionizing the way products are designed and manufactured. With their commitment to innovation, customer satisfaction, and environmental responsibility, they are well-positioned to lead the way towards a future where 3D printing is the norm. As the industry evolves, Prototype Molds will undoubtedly remain at the forefront, driving innovation and shaping the future of additive manufacturing.
Enhance Your Precision Machining with Advanced 4-Axis Lathe Technology
Title: Advanced 4-Axis Lathe Unveiled by Prominent ManufacturerIntroduction:In a bid to revolutionize the machining industry, a renowned machinery manufacturer who specializes in precision engineering has recently introduced a cutting-edge 4-axis lathe (Name omitted for confidentiality). This state-of-the-art machine is set to redefine machining capabilities by offering enhanced precision, increased productivity, and superior machining quality. With its unique features and advanced technology, this new lathe promises to deliver exceptional performance, catering to a diverse range of industries and applications.Body:1. Overview of the 4-axis lathe:The newly launched lathe embodies the manufacturer's commitment to innovation and excellence. With its cutting-edge 4-axis design, the lathe offers increased flexibility, enabling more complex machining operations. Equipped with advanced control systems, this lathe is capable of performing continuous and simultaneous machining on four different axes, revolutionizing traditional machining processes. This innovative approach significantly reduces production time while ensuring high accuracy and precision.2. Key features and benefits:The 4-axis lathe boasts a range of features designed to optimize efficiency and productivity. Its exceptional capabilities include:- Multi-axis simultaneous machining: With the ability to perform precise and synchronized operations on four axes, the lathe can handle complex geometries and achieve intricate machining tasks.- Enhanced precision and accuracy: The advanced control systems ensure highly precise movements and accurate machining, resulting in superior product quality and tolerances.- Improved tooling options: The lathe incorporates a versatile tooling system, allowing for easy tool changes and increasing workflow efficiency.- Higher productivity: By executing simultaneous operations, the lathe minimizes idle time, maximizing production throughput and reducing overall manufacturing costs.- User-friendly interface: The intuitive control panel and user interface make operation and programming convenient and easy for operators of varied skill levels.- Safety features: The lathe is equipped with state-of-the-art safety mechanisms, ensuring operators can work safely, avoiding accidents and injuries.- Durability and reliability: Built with top-grade materials and rigorous quality control, the lathe guarantees high durability and long-term reliability, minimizing downtime.3. Applications and industries served:The 4-axis lathe is designed to cater to a wide spectrum of industries and machining needs. Some of the key sectors that can benefit from this cutting-edge machinery include aerospace, automotive, medical equipment manufacturing, electronics, and defense. The lathe's versatility and precision make it an invaluable asset for producing intricate components, prototypes, and complex parts requiring high dimensional accuracy.4. Company's commitment to innovation:With its groundbreaking 4-axis lathe, the manufacturer continues its tradition of pushing the boundaries of machining technology. Known for its dedication to research and development, the company has aimed to deliver advanced solutions that adapt to the evolving needs of the industry. By incorporating the latest innovations into their machinery, they consistently offer state-of-the-art products that boost productivity, reduce costs, and maximize operational efficiency for their clients.Conclusion:As the machinery industry continues to evolve, the introduction of the advanced 4-axis lathe by this leading manufacturer marks a significant milestone. This cutting-edge lathe is set to redefine machining capabilities by offering enhanced precision, increased productivity, and superior machining quality. With its versatile features and user-friendly operation, this 4-axis lathe is poised to become an indispensable tool for various industries, catering to their diverse machining needs. The manufacturer's commitment to innovation reinforces their position as an industry leader, consistently delivering groundbreaking solutions to propel the machining sector into the future.
Exploring the Benefits of Aluminum Injection Molding in Today's Manufacturing Industry
[Assistant]Title: Revolutionizing Manufacturing: Aluminum Injection Molding Sets New Industry StandardsIntroduction:Innovation continues to be the driving force behind advancements in the manufacturing industry. Among the latest breakthroughs is the revolutionary technique of aluminum injection molding. This cutting-edge manufacturing process has the potential to reshape various sectors by providing unique advantages such as cost-effectiveness, increased design flexibility, and enhanced production efficiency. In this article, we delve into the details of aluminum injection molding, exploring its benefits, applications, and the promising future it holds.Understanding Aluminum Injection Molding:Aluminum injection molding is an advanced manufacturing technique that combines the versatility of plastic injection molding with lightweight and durable aluminum materials. This process involves injecting molten aluminum under high pressure into complex and intricate molds, allowing for the creation of intricate parts and components with exceptional precision. The process takes advantage of the desirable properties of aluminum, including its high strength-to-weight ratio, corrosion resistance, and excellent thermal conductivity.The Company's Role:The trailblazers in aluminum injection molding technology, [Company Name], have been at the forefront of the industry, leading in research, development, and implementation of this groundbreaking method. Their extensive experience and cutting-edge facilities have enabled them to refine and perfect the aluminum injection molding process, making it highly efficient and adaptable to various manufacturing requirements. The company's dedication to continuous innovation has positioned them as a driving force behind the widespread adoption of aluminum injection molding.Applications and Industries Transformed:The advent of aluminum injection molding has had a transformative impact across numerous industries, offering a wide range of applications and benefits. In the automotive sector, lightweight aluminum components produced through this process have revolutionized vehicle design, leading to improved fuel efficiency, better performance, and enhanced safety. Similarly, aerospace manufacturers are benefiting from the lightweight properties of aluminum injection-molded parts, resulting in reduced fuel consumption and increased payload capabilities.Electronics and telecommunications industries can leverage the design flexibility of aluminum injection molding to create intricate and high-performance electronic enclosures and housings. The process also allows for the integration of additional features, such as heat sinks, resulting in improved thermal management and extended device lifespans.The medical field is yet another sector where aluminum injection molding can make a profound impact. The ability to produce complex and sterile medical devices and implants made from lightweight yet durable aluminum materials opens new possibilities for enhanced patient care, improved surgical outcomes, and cost-effective medical solutions.Benefits Driving Adoption:The widespread adoption of aluminum injection molding can be attributed to the numerous benefits it offers. One of the most significant advantages is the cost-effectiveness of the process. By utilizing aluminum materials, which are relatively inexpensive, manufacturers can produce lightweight yet strong components without breaking the bank. This affordability extends to the tooling process as well, as aluminum molds are generally less costly than traditional injection molding molds.Moreover, aluminum injection molding enables manufacturers to achieve intricate and precise designs that were previously unattainable. The ability to create complex geometries with exceptional accuracy allows for the integration of multiple functions into a single part, reducing assembly time and enhancing overall product performance.Furthermore, the lightweight nature of aluminum components facilitates transportation and logistics, ultimately reducing costs and environmental impact. Aluminum's corrosion resistance properties also ensure long-lasting durability, making it an ideal choice for applications exposed to harsh environments or demanding conditions.The Path Towards a Promising Future:As aluminum injection molding continues to gain traction, researchers and manufacturers are working collaboratively to push its boundaries further. The ongoing advancement of this technology aims to enhance process efficiency, minimize cycle times, and explore possibilities for new alloy variants. Additionally, efforts are being made to streamline post-processing techniques such as surface treatments and finishing processes to ensure the highest quality standards.Industry experts predict that aluminum injection molding will play a pivotal role in the wider adoption of electric vehicles, thanks to the efficiency gains and material advantages it offers. Furthermore, as sustainability and lightweighting remain key focus areas for many industries, aluminum injection molding will likely continue to grow, revolutionizing diverse sectors such as consumer electronics, renewable energy, and industrial manufacturing.Conclusion:Aluminum injection molding represents a transformative leap in the manufacturing industry. This innovative technique has revolutionized product design and production, with its cost-effectiveness, design flexibility, and lightweight yet durable results. Spearheaded by industry leaders like [Company Name], aluminum injection molding is poised to reshape diverse sectors, promising a future characterized by enhanced efficiency, improved performance, and sustainable manufacturing practices. As research and development continue to progress, the prospects for this revolutionary method are boundless.
Silicone Rubber Parts: Latest Developments in High-Quality Manufacturing
Silicone Rubber Parts Revolutionizing Industries: An Introduction to [Company Name][City, Date] - Silicone rubber parts have emerged as a revolutionary solution across a wide range of industries, providing unparalleled versatility and performance. [Company Name] has been at the forefront of this innovation, offering cutting-edge silicone rubber parts that are transforming various sectors. With a commitment to delivering superior quality and unmatched customer satisfaction, [Company Name] has become a trusted name in the silicone rubber industry.Since its establishment [number of years] ago, [Company Name] has dedicated itself to research, development, and production of high-quality silicone rubber parts. Backed by a team of experienced engineers and designers, the company continues to push boundaries and redefine the possibilities of silicone rubber applications. Their relentless pursuit of innovation has paved the way for groundbreaking solutions in industries such as automotive, electronics, healthcare, aerospace, and many more.The automotive industry, in particular, has witnessed remarkable advancements in the use of silicone rubber parts. From gaskets and seals to custom molded components, silicone rubber offers exceptional resistance to temperature, chemicals, and wear. [Company Name] has been instrumental in providing automotive manufacturers with tailor-made solutions that enhance performance, durability, and safety.In the electronics sector, where precision and reliability are of utmost importance, silicone rubber parts from [Company Name] play a vital role. These parts are instrumental in protecting sensitive electronic components from harsh environments, such as moisture, dust, and vibration. They also provide excellent electrical insulation properties, ensuring the longevity and functionality of electronic devices.Furthermore, the healthcare industry has seen a surge in the adoption of silicone rubber parts due to their biocompatibility and sterilization capabilities. Silicone rubber has become the material of choice for medical devices, implants, and equipment, thanks to its hypoallergenic nature and resistance to bacteria growth. [Company Name]'s expertise in this field has helped healthcare professionals and patients alike, ensuring the highest standards of safety and performance.Silicone rubber parts developed by [Company Name] have found their way into the aerospace industry as well. With stringent requirements for high-temperature resistance and durability, silicone rubber parts offer unmatched reliability in critical aerospace applications. Whether it's seals for engines, gaskets for compartments, or vibration-dampening mounts, [Company Name] has demonstrated its ability to meet and exceed the demands of this challenging industry.What sets [Company Name] apart from others in the market is its commitment to customization. The company understands that every industry and application has unique requirements, and a one-size-fits-all approach simply won't suffice. With state-of-the-art manufacturing facilities and advanced production techniques, [Company Name] ensures that each silicone rubber part is precisely engineered to the customer's exact specifications.Moreover, [Company Name] places emphasis on quality control, adhering to the highest industry standards. Rigorous testing procedures and inspections are carried out at every stage of the production process, guaranteeing that only flawless silicone rubber parts reach the customers. This unwavering commitment to quality has earned [Company Name] a reputation for excellence and reliability in the industry.Looking ahead, [Company Name] continues to drive innovation and explore new possibilities in silicone rubber applications. With ongoing research and development, the company aims to push the boundaries of what silicone rubber can achieve and uncover solutions for even the most challenging applications. [Company Name] is poised to shape the future of industries, offering products that are not only functional but also environmentally friendly and sustainable.In conclusion, silicone rubber parts have become a game-changer across various industries, with [Company Name] leading the charge in innovation and quality. With their unrivaled expertise and customer-centric approach, [Company Name] has solidified itself as a trusted partner for businesses looking to leverage the full potential of silicone rubber in their operations. As the demand for high-performance and reliable solutions continues to grow, [Company Name] remains committed to exceeding customer expectations and pioneering the silicone rubber revolution.Contact:[Company Name][Address][Phone Number][Email][Website]
Revolutionizing Injection Molding: Efficiencies and Advancements Unveiled
[Assistant]Title: Innovative Injection Molds Revolutionize Manufacturing Process in the Plastic IndustryIntroduction:In the rapidly evolving world of manufacturing, injection molding has emerged as a game-changer, enabling the mass production of plastic products. With advanced technology and relentless dedication to innovation, [Company Name] has developed groundbreaking injection molds that are poised to revolutionize the industry. These molds not only streamline the manufacturing process but also enhance efficiency, quality, and customization options. By combining cutting-edge techniques with a commitment to sustainable practices, [Company Name] is redefining the way plastic products are manufactured.Body:1. Introduction to Injection Molding:Injection molding is a manufacturing process that involves injecting molten material, such as plastic, into a mold cavity. The molten material solidifies inside the mold, resulting in a precisely shaped, high-quality finished product. This process has gained immense popularity due to its ability to produce a wide range of products in large quantities, making it ideal for industries such as automotive, aerospace, consumer goods, and more.2. [Company Name]'s Innovative Approach to Injection Molding:Recognizing the potential of injection molding to transform the plastic industry, [Company Name] has taken innovative strides to push the boundaries of this technology. They have developed state-of-the-art injection molds that incorporate cutting-edge features, offering numerous advantages over traditional molds.3. Enhanced Efficiency and Precision:[Company Name]'s injection molds are engineered to optimize efficiency and precision. Through meticulous design and advanced manufacturing techniques, these molds facilitate faster cooling times, reducing production cycles and increasing productivity. Additionally, their molds incorporate advanced cavity and core design, resulting in superior product accuracy, eliminating the need for excessive post-production processes.4. Customization and Flexibility:Acknowledging the increasing demand for customized plastic products, [Company Name] has developed injection molds that provide unprecedented customization options. By leveraging their expertise in mold design and engineering, they offer clients the ability to create intricate and complex designs, meeting diverse requirements and surpassing expectations.5. Sustainability and Environmental Considerations:In keeping with the growing sustainability trends in the manufacturing industry, [Company Name] places a strong emphasis on eco-friendly practices. Their injection molds utilize advanced materials that reduce energy consumption and minimize waste generation, contributing to a greener manufacturing process. By integrating sustainable techniques, [Company Name] aims to establish itself as a responsible and environmentally-conscious industry leader.6. Collaborative Approach and Customer Satisfaction:[Company Name] believes in fostering strong partnerships with their clients. They work closely with manufacturers to understand their specific needs and offer tailored solutions. By providing comprehensive technical support and excellent after-sales service, [Company Name] ensures customer satisfaction at every stage of the manufacturing process.7. Competing in a Global Market:[Company Name] has set its sights on capturing a significant share of the global injection mold market. By leveraging their cutting-edge technology, commitment to innovation, and a highly skilled workforce, they are well-positioned to meet the increasing demand for high-quality, efficient, and customizable injection molding solutions.Conclusion:With their revolutionary injection molds, [Company Name] is poised to transform the plastic industry. By enhancing efficiency, precision, and customization options, they are reshaping the way plastic products are manufactured. Through their commitment to sustainability and customer satisfaction, [Company Name] has firmly established itself as a frontrunner in the global injection mold market. As the industry continues to evolve, [Company Name] will remain at the forefront, driving innovation and pushing the boundaries to meet the ever-growing demands of manufacturers worldwide.
Discover the Benefits of Sheet Metal Prototypes for Efficient Product Development
Sheet Metal Prototypes Launches Innovative Metal Fabrication Service[Company City, State] - Sheet Metal Prototypes, a leading provider of metal fabrication solutions, is excited to announce the launch of a groundbreaking metal fabrication service that combines cutting-edge technology with extensive expertise in sheet metal production.With over [number of years] years of experience in the industry, Sheet Metal Prototypes has established itself as a trusted partner for businesses looking for high-quality metal components. Their latest innovation showcases their commitment to staying at the forefront of metal fabrication technology.The new metal fabrication service offered by Sheet Metal Prototypes utilizes advanced techniques to produce precise, reliable, and durable metal prototypes. Through computer-aided design (CAD) software and state-of-the-art machinery, their team of skilled engineers can create complex metal parts with unparalleled accuracy."We are thrilled to introduce this cutting-edge metal fabrication service to our clients," said [Company Spokesperson], [Position] at Sheet Metal Prototypes. "Our goal has always been to provide the highest level of quality and precision in our fabricated metal parts, and this new service allows us to take that commitment to the next level."The use of CAD software allows for seamless integration between design and fabrication, eliminating potential errors and ensuring consistent results. Clients can now see virtual renderings of their metal prototypes before they are produced, streamlining the design process and minimizing the risk of costly revisions.Sheet Metal Prototypes' state-of-the-art machinery includes laser cutting systems, CNC punching machines, and press brakes, among others. Each piece of equipment is meticulously maintained to provide optimal performance and enhanced efficiency during the fabrication process.The company's team of highly skilled and experienced engineers collaborates closely with clients, offering extensive knowledge and guidance throughout the metal fabrication process. From design consultations to material selection and prototype development, their expertise ensures that clients receive tailor-made solutions that meet their specific requirements."We understand that every project is unique, and that's why we place great emphasis on close collaboration with our clients," added [Company Spokesperson]. "Our team is dedicated to providing personalized service and delivering high-quality metal prototypes that exceed expectations."Sheet Metal Prototypes' commitment to environmental sustainability is also evident in their metal fabrication service. By employing efficient manufacturing practices and utilizing recyclable materials, they aim to minimize their impact on the environment. The company adheres to strict quality control standards, ensuring that each metal prototype is thoroughly inspected before final delivery.As the demand for precision metal components continues to grow across various industries, Sheet Metal Prototypes remains dedicated to pushing the boundaries of metal fabrication technology. With their innovative service, they have solidified their position as a trusted partner for businesses seeking reliable and high-quality metal prototypes.To learn more about Sheet Metal Prototypes' groundbreaking metal fabrication service, visit their website [website URL] or contact their team at [contact information].About Sheet Metal Prototypes:Sheet Metal Prototypes is a leading provider of metal fabrication solutions, specializing in the production of high-quality metal prototypes. With over [number of years] years of industry experience, their team of skilled engineers combines advanced technology with personalized service to deliver precision-crafted metal parts that meet clients' exact specifications. The company is committed to environmental sustainability and employs eco-friendly practices throughout the fabrication process.
Benefits of Rapid Injection Molding for Quick and Affordable Production
Rapid Injection Molding: Revolutionizing Manufacturing ProcessesIn today's fast-paced world, innovation is a key driver of success. Companies are constantly seeking ways to improve their manufacturing processes, reduce time to market, and stay ahead of the competition. One of the most groundbreaking advancements in this regard is Rapid Injection Molding, a technology that has revolutionized the way products are designed and produced.At the forefront of this game-changing technology is a leading manufacturing company. With a strong emphasis on innovation and cutting-edge solutions, the company has established itself as a pioneer in the field of Rapid Injection Molding. By leveraging state-of-the-art equipment, advanced materials, and a highly skilled team, they have set a new standard for speed, precision, and efficiency in the industry.Rapid Injection Molding is a process that enables the rapid production of high-quality, precision-engineered plastic parts. Unlike traditional injection molding methods, which can be time-consuming and cost-prohibitive, Rapid Injection Molding offers a faster and more cost-effective solution. This is achieved through the use of advanced technology and streamlined production processes, allowing for quick turnaround times and reduced lead times.One of the key advantages of Rapid Injection Molding is its ability to significantly accelerate the product development cycle. By reducing the time required for tooling and production, companies can bring their products to market much faster, giving them a competitive edge in today's dynamic business environment. This not only allows for quicker product launches but also enables companies to respond more effectively to changing market demands and customer needs.Furthermore, Rapid Injection Molding offers unparalleled design flexibility. With the ability to quickly create and modify molds, companies can easily iterate on their designs and prototypes, leading to improved product quality and performance. This level of agility is essential in industries where innovation and differentiation are critical to success.In addition to speed and flexibility, Rapid Injection Molding also delivers exceptional quality and precision. The advanced technology and expertise employed by the company ensure that each part meets the strictest tolerances and specifications. This level of precision is essential for industries such as aerospace, automotive, medical devices, and consumer electronics, where reliability and performance are non-negotiable.Moreover, Rapid Injection Molding is a more sustainable and eco-friendly alternative to traditional manufacturing methods. By optimizing production processes and minimizing material waste, companies can reduce their environmental footprint and contribute to a more sustainable future.As a result of these benefits, Rapid Injection Molding has garnered widespread attention and adoption across various industries. Companies are increasingly turning to this technology to gain a competitive edge, reduce costs, and accelerate their time to market. With the demand for rapid and cost-effective manufacturing solutions on the rise, Rapid Injection Molding is poised to play an even more significant role in the future of production.In conclusion, Rapid Injection Molding is a game-changer that is revolutionizing the manufacturing landscape. With its ability to deliver speed, flexibility, precision, and sustainability, it has become a vital tool for companies looking to stay ahead in today's competitive market. As companies continue to embrace this cutting-edge technology, the possibilities for innovation and advancement are endless. The company's commitment to excellence and innovation will undoubtedly position them at the forefront of this transformative trend, shaping the future of manufacturing for years to come.