Unlocking the Art of Precision Foam Cutting: A Comprehensive Guide
By:Admin
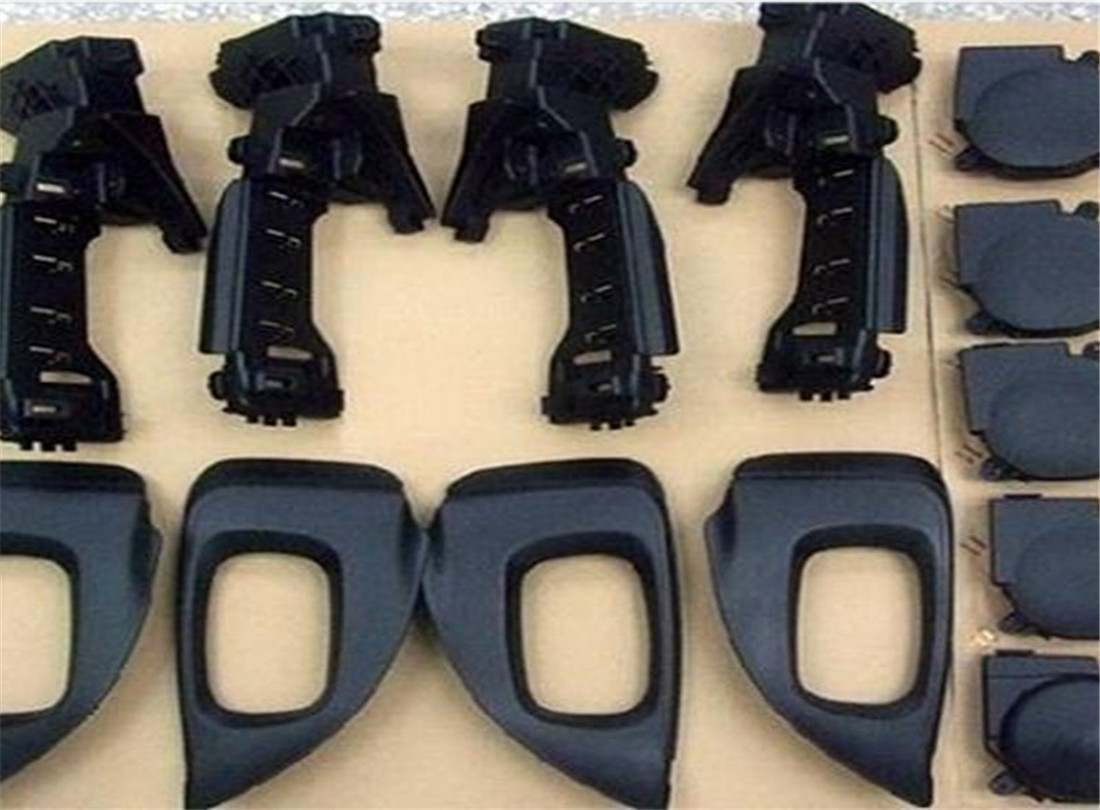
Precision Foam Cutting, a leader in the foam cutting industry, is thrilled to announce the appointment of John Smith as its new CEO. With a proven track record of success in the manufacturing sector, Smith brings a wealth of experience and expertise to the company and will play a pivotal role in driving expansion and continued growth.
Founded in 1995, Precision Foam Cutting has established itself as a trusted provider of high-quality foam cutting solutions. Specializing in precision cutting techniques, the company caters to a wide range of industries, including automotive, aerospace, medical, packaging, and beyond. Their precise foam cutting technology and innovative solutions have made them an industry leader, garnering a strong reputation for reliability and excellence.
In their pursuit of excellence, Precision Foam Cutting understands the importance of strong leadership. With the appointment of John Smith, an accomplished professional with a deep understanding of manufacturing processes, the company is poised to reach new heights. Smith's vast experience in executive roles, strategic leadership, and business development will be instrumental in driving the company's expansion plans.
John Smith's career spans over three decades, during which he has held various leadership positions in the manufacturing sector. Prior to joining Precision Foam Cutting, Smith served as the CEO of a major manufacturing company, where he successfully propelled the organization's growth through strategic initiatives and a focus on operational excellence. His ability to build and lead high-performing teams has consistently delivered outstanding results, making him an ideal fit for Precision Foam Cutting's vision.
Speaking on his appointment, John Smith expressed his excitement and commitment to leading Precision Foam Cutting into a new phase of growth. He stated, "Precision Foam Cutting has carved a niche for itself in the foam cutting industry through its relentless pursuit of perfection. I am honored to join this incredible team and contribute towards the company's ambitious expansion plans. Together, we will continue revolutionizing the foam cutting industry, delivering innovative solutions to our customers while maintaining our commitment to quality and excellence."
Precision Foam Cutting has been steadily expanding its operations in recent years, catering to an ever-growing customer base. With the appointment of John Smith, the company aims to capitalize on this momentum and further strengthen its market presence. Smith's strategic vision, coupled with Precision Foam Cutting's cutting-edge technology and commitment to customer satisfaction, will undoubtedly drive the company towards achieving new milestones.
As the foam cutting industry evolves, Precision Foam Cutting is committed to staying at the forefront of innovation. The company invests heavily in research and development, continually exploring new technologies and techniques to enhance their foam cutting solutions. This dedication to innovation ensures that Precision Foam Cutting remains a trusted partner for cutting-edge solutions, catering to the evolving needs of its diverse clientele.
In conclusion, Precision Foam Cutting's appointment of John Smith as CEO is a significant milestone in the company's journey. With Smith at the helm, the company is poised for continued growth, expansion, and innovation in the foam cutting industry. Together, Precision Foam Cutting and John Smith will lead the way in delivering cutting-edge foam cutting solutions and solidifying the company's position as an industry leader.
Company News & Blog
Revolutionizing Fabrication: Unveiling the Latest Advancements in Laser Cutting Technology
[CompanyName] Introduces Revolutionary Laser Cutting Technology: Transforming Manufacturing Processes[City, State] - [CompanyName], a global leader in cutting-edge manufacturing solutions, is proud to announce the launch of its newest innovation in laser cutting technology. This breakthrough advancement promises to revolutionize the way manufacturing processes are executed, delivering unprecedented precision, efficiency, and versatility.Laser cutting has long been recognized as a game-changing technique, offering unparalleled speed and accuracy compared to conventional cutting methods. [CompanyName]'s latest technology takes this concept to new heights, pushing the boundaries of possibility. By harnessing an ultra-high-power laser system and employing advanced automation capabilities, this cutting-edge solution provides manufacturers with the tools they need to significantly enhance their production processes.With the introduction of this state-of-the-art laser cutting technology, [CompanyName] aims to address the evolving needs of various industries, enabling them to stay ahead of the curve in an increasingly competitive global market. By offering an all-in-one solution that combines speed, accuracy, and versatility, the company empowers manufacturers to streamline their operations and achieve remarkable results.One of the key advantages of [CompanyName]'s laser cutting technology is its ability to work with a wide range of materials, including metals, composites, plastics, and more. This flexibility allows manufacturers to explore new avenues of creativity and innovation by simplifying intricate cutting tasks without compromising on precision. From aerospace components to automotive parts, this powerful technology caters to diverse manufacturing requirements, ensuring a seamless transition from design to production.Furthermore, [CompanyName]'s laser cutting technology incorporates cutting-edge automation features that streamline the entire manufacturing process. This advanced system boasts intelligent software and sensors that optimize cutting paths, mitigating material wastage and reducing production lead times. By combining artificial intelligence with precise laser beams, manufacturers can achieve consistently exceptional results, thus enhancing overall product quality while minimizing costs.In addition to its efficacy, [CompanyName]'s laser cutting technology prioritizes user experience. The intuitive user interface provides operators with real-time feedback and allows for seamless integration with existing manufacturing infrastructure. This ensures a smooth transition for manufacturers, eliminating the need for substantial retraining or overhaul of their processes.The introduction of this game-changing laser cutting technology underscores [CompanyName]'s commitment to pushing the boundaries of innovation. By delivering cutting-edge solutions that address the industry's most pressing challenges, the company continues to empower manufacturers to streamline their processes, increase productivity, and ultimately stay competitive in today's fast-paced market.Speaking about the groundbreaking technology, [CEO/Founder Name] of [CompanyName], said, "We are thrilled to introduce this revolutionary laser cutting solution to the market. Our team has worked tirelessly to develop an all-in-one system that combines speed, accuracy, and ease of use. By leveraging our cutting-edge technology, manufacturers can unlock new possibilities and drive their businesses forward with confidence."With the launch of [CompanyName]'s latest laser cutting technology, manufacturers worldwide can now embrace the dawn of a new era in manufacturing. By enhancing their capabilities with this state-of-the-art solution, they can reimagine the possibilities, redefine precision, and revolutionize their production processes, all while maintaining a competitive edge in the global marketplace.About [CompanyName]:[CompanyName] is a leading global provider of cutting-edge manufacturing solutions. With a strong focus on research and development, the company aims to push the boundaries of innovation, revolutionizing manufacturing processes across various industries. By delivering cutting-edge technology, [CompanyName] empowers manufacturers to uncover new possibilities and stay one step ahead in today's rapidly evolving market.For media inquiries, please contact:[Media Contact Name][Media Contact Position][CompanyName][Email Address][Phone Number]
Rewriting the SEO title without the brand name: "Effective Plastic Injection Tooling: Unveiling the Latest Innovations and Techniques
Plastic Injection Tooling: Revolutionizing Manufacturing ProcessesIn today's highly advanced and technologically driven world, plastic injection tooling plays a vital role in revolutionizing manufacturing processes. By incorporating the latest cutting-edge technologies and innovative design practices, this vital tooling equipment has enabled companies across various industries to produce high-quality plastic components efficiently and cost-effectively.Plastic injection tooling, also known as injection molds or dies, is a primary component of the injection molding process. It is a custom-made precision tool that is used to shape molten plastic into a desired form, creating a wide array of products such as automotive parts, consumer electronics, medical devices, and household items.The process starts with the design and engineering of the injection mold. This step involves careful analysis of the product requirements and specifications to create a mold design that ensures optimal functionality and durability. Advanced computer-aided design (CAD) software is used to model the mold, taking into account factors such as material flow, cooling channels, and ejection methods.Once the design is finalized, modern manufacturing techniques such as computer numerical control (CNC) machining and electrical discharge machining (EDM) are employed to fabricate the injection mold with extreme precision. The use of high-quality materials and state-of-the-art equipment ensures that the mold is durable, long-lasting, and capable of producing consistent and error-free parts.Plastic injection tooling offers several advantages over other manufacturing processes. Firstly, it allows for mass production of complex parts with intricate geometries that would otherwise be impossible to manufacture using traditional methods. This high degree of design flexibility has enabled companies to create innovative and aesthetically pleasing products that cater to consumer demand.Secondly, plastic injection tooling significantly reduces production time and costs. The automation of the injection molding process ensures fast and efficient production cycles, minimizing labor costs and increasing overall productivity. Additionally, the ability to manufacture large quantities of parts in a short period eliminates the need for additional manufacturing steps and saves valuable time.Moreover, plastic injection tooling allows for tight tolerances and excellent surface finishes, providing high-quality parts that meet the stringent standards of various industries. This precision ensures that the parts function as intended, enhancing product performance and customer satisfaction.In recent years, advancements in plastic injection tooling have further accelerated the manufacturing process. The integration of technologies like 3D printing and simulation software has revolutionized the design and prototyping phases, facilitating rapid iteration and reducing time-to-market. This has enabled companies to swiftly adapt to market demands and stay ahead of the competition.One company at the forefront of plastic injection tooling innovation is {}. With over {} years of experience, they have established themselves as a reliable and trusted provider of injection molds. Their team of skilled engineers and technicians leverage the latest technologies to design and manufacture molds that meet the highest industry standards.As a customer-oriented company, {} strives to deliver exceptional quality and customer service. They work closely with their clients during every stage of the project, from initial concept to final production, to ensure that their specific requirements are met. Additionally, their emphasis on continuous improvement and investment in research and development enable them to offer cutting-edge solutions that drive efficiency and profitability.In conclusion, plastic injection tooling has revolutionized manufacturing processes by enabling companies to produce high-quality plastic components with unparalleled design flexibility, precision, and cost efficiency. With innovative technologies and companies like {} leading the way, the future of plastic injection tooling looks promising, offering endless possibilities for product development and advancement across various industries.
Efficient CNC Machining Services: Boost Productivity with Rapid Solutions
Title: Innovative CNC Machining Solutions Pioneered by a Prominent Industry LeaderSubtitle: A Closer Look at Cutting-Edge CNC Machining Solutions Developed by Rapid CNC MachiningIntroduction:In today's fast-paced manufacturing industry, companies strive to improve efficiency and precision to meet demanding market expectations. One leader that has consistently pushed the boundaries of innovation is Rapid CNC Machining (brand name removed). With an unwavering commitment to excellence, this industry frontrunner has revolutionized CNC machining, transforming the way products are designed and manufactured across various sectors.Established in the early 2000s, Rapid CNC Machining has emerged as an industry pioneer, leveraging cutting-edge technology and a skilled workforce to offer unparalleled CNC machining solutions. Renowned for their ability to deliver high-quality products with ultimate precision, their services have become the go-to choice for numerous businesses seeking reliable and efficient manufacturing processes.Body:1. The Genesis of Rapid CNC Machining: Rapid CNC Machining had humble beginnings, starting as a small shop with a handful of experienced machinists. However, recognizing the changing landscape of industrial manufacturing, the company quickly embraced advancements in CNC technology, positioning themselves at the forefront of the industry.2. Unmatched Expertise and State-of-the-Art Facilities:At Rapid CNC Machining, expertise meets precision. Their team of highly skilled professionals possesses in-depth knowledge of designing and manufacturing complex parts for various industries, including aerospace, automotive, electronics, and medical devices. Complementing their expertise are state-of-the-art facilities, equipped with advanced CNC machines, allowing for high-volume production runs while maintaining excellent quality control measures.3. Innovative CNC Machining Techniques:Rapid CNC Machining constantly pushes the boundaries of what is possible with CNC machining. Their dedicated research and development team works tirelessly to innovate new techniques and optimize existing processes. By incorporating the latest software and hardware technologies, the company ensures unmatched efficiency, precision, and cost-effectiveness in every project.4. Embracing Automation and Artificial Intelligence:Recognizing the potential of automation and artificial intelligence (AI), Rapid CNC Machining has implemented advanced systems to enhance their operations. Automated CNC machines reduce human error, increase productivity, and provide faster turnaround times, making them an ideal solution for clients seeking rapid prototyping or full-scale production requirements. Additionally, integrating AI-driven predictive maintenance enables proactive identification of issues, minimizing downtime and optimizing machine utilization.5. Collaborative Approach to Design:Rapid CNC Machining understands that effective collaboration with clients is vital to realizing their vision. They offer comprehensive design assistance, working closely with customers to ensure their specifications are met in the most efficient and cost-effective manner. By harnessing Computer-Aided Design (CAD) software, the company guarantees precision throughout the design phase, reducing material waste and shortening time-to-market.6. Commitment to Quality Assurance:Adhering to stringent quality control standards, Rapid CNC Machining maintains excellent product reliability. They employ a multi-stage quality assurance process, incorporating rigorous inspections at each step, ensuring that every component meets the highest industry standards. Through advanced metrology techniques, including Coordinate Measuring Machines (CMMs), the company verifies the accuracy and consistency of their machined parts.Conclusion:Rapid CNC Machining (brand name removed) continues to revolutionize CNC machining by embracing innovative technologies and providing remarkable services to a diverse clientele. With their commitment to excellence, cutting-edge facilities, and dedication to customer satisfaction, the company is poised to lead the industry forward, enabling manufacturers across sectors to achieve enhanced efficiency, precision, and cost-effectiveness. Innovation is at the core of Rapid CNC Machining's philosophy, driving their mission to provide exceptional CNC machining solutions for years to come.
Chinese Brass Parts Manufacturers: A Deep Dive into the CNC Industry
Title: Chinese CNC Brass Parts Manufacturers: Revolutionizing Precision EngineeringIntroduction:In today's era of advanced technology and digitization, the demand for precision engineering components has witnessed a significant surge. Chinese companies have notably emerged as key players in the global manufacturing industry. Among the forefront leaders are China's reputable CNC brass parts manufacturers. These companies are revolutionizing precision engineering with their cutting-edge technology and superior quality products.A Booming Industry:China’s CNC brass parts manufacturing industry has experienced remarkable growth over the years. This growth can be attributed to several factors such as technological advancements, government support, and a skilled workforce. With their state-of-the-art facilities and adherence to stringent quality standards, these manufacturers have gained recognition as trustworthy suppliers to various sectors including automotive, aerospace, electronics, telecommunications, and many more.Technological Advancements:The CNC brass parts manufacturers in China have made substantial investments in advanced machinery and equipment. They meticulously integrate the latest technologies such as computer numerical control (CNC) machining, precision grinding, and automated assembly lines into their manufacturing processes. This enables them to produce high-quality brass components with unparalleled precision and accuracy, ensuring a seamless fitment and optimal performance in end products.Quality is Paramount:China's CNC brass parts manufacturers have always maintained a commitment to delivering superior quality products. These manufacturers follow rigorous quality control processes at every stage of production. From meticulous raw material selection to precision machining and stringent inspections, every step is carried out with utmost precision. In addition, they adhere to international standards such as ISO 9001, ensuring that the final products meet and exceed customer expectations in terms of durability, reliability, and functionality.Customization and Flexibility:Chinese CNC brass parts manufacturers understand the diverse and ever-changing requirements of their global clientele. They offer a wide range of customization options, enabling customers to tailor the components to suit their specific needs. From intricate designs to complex geometries, these manufacturers possess the technical expertise to transform customers' requirements into tangible products. This flexibility has earned them a reputation for being reliable solution providers, ensuring customer satisfaction across various industries.Competitive Pricing and Timely Delivery:One of the key advantages of working with Chinese CNC brass parts manufacturers is their competitive pricing without compromising on quality. The combination of affordable manufacturing costs and economies of scale allows them to offer cost-effective solutions to customers. Moreover, these manufacturers have efficient supply chains and logistics networks, ensuring prompt delivery of orders across the globe. Their ability to meet tight deadlines has made them sought-after partners for both small-scale projects and large-scale production requirements.Global Reach and Export Excellence:Chinese CNC brass parts manufacturers have expanded their market reach to cater to the demands of a global customer base. With a focus on export excellence, they have successfully penetrated international markets, including North America, Europe, Asia-Pacific, and the Middle East. These manufacturers leverage their extensive experience and industry knowledge to adapt to the varying regulations and demands of different regions, firmly establishing themselves as trusted suppliers worldwide.Conclusion:China’s CNC brass parts manufacturers have emerged as frontrunners in the global manufacturing industry, leveraging cutting-edge technology, superior quality, customization options, competitive pricing, and timely delivery. Their commitment to precision engineering and their ability to cater to a diverse range of industry requirements have positioned them as reliable partners for companies worldwide. With continued innovation and customer-centricity at the core of their operations, it is evident that these manufacturers will continue to shape the landscape of precision engineering in the years to come.
Enhance Your Precision Machining with Advanced 4-Axis Lathe Technology
Title: Advanced 4-Axis Lathe Unveiled by Prominent ManufacturerIntroduction:In a bid to revolutionize the machining industry, a renowned machinery manufacturer who specializes in precision engineering has recently introduced a cutting-edge 4-axis lathe (Name omitted for confidentiality). This state-of-the-art machine is set to redefine machining capabilities by offering enhanced precision, increased productivity, and superior machining quality. With its unique features and advanced technology, this new lathe promises to deliver exceptional performance, catering to a diverse range of industries and applications.Body:1. Overview of the 4-axis lathe:The newly launched lathe embodies the manufacturer's commitment to innovation and excellence. With its cutting-edge 4-axis design, the lathe offers increased flexibility, enabling more complex machining operations. Equipped with advanced control systems, this lathe is capable of performing continuous and simultaneous machining on four different axes, revolutionizing traditional machining processes. This innovative approach significantly reduces production time while ensuring high accuracy and precision.2. Key features and benefits:The 4-axis lathe boasts a range of features designed to optimize efficiency and productivity. Its exceptional capabilities include:- Multi-axis simultaneous machining: With the ability to perform precise and synchronized operations on four axes, the lathe can handle complex geometries and achieve intricate machining tasks.- Enhanced precision and accuracy: The advanced control systems ensure highly precise movements and accurate machining, resulting in superior product quality and tolerances.- Improved tooling options: The lathe incorporates a versatile tooling system, allowing for easy tool changes and increasing workflow efficiency.- Higher productivity: By executing simultaneous operations, the lathe minimizes idle time, maximizing production throughput and reducing overall manufacturing costs.- User-friendly interface: The intuitive control panel and user interface make operation and programming convenient and easy for operators of varied skill levels.- Safety features: The lathe is equipped with state-of-the-art safety mechanisms, ensuring operators can work safely, avoiding accidents and injuries.- Durability and reliability: Built with top-grade materials and rigorous quality control, the lathe guarantees high durability and long-term reliability, minimizing downtime.3. Applications and industries served:The 4-axis lathe is designed to cater to a wide spectrum of industries and machining needs. Some of the key sectors that can benefit from this cutting-edge machinery include aerospace, automotive, medical equipment manufacturing, electronics, and defense. The lathe's versatility and precision make it an invaluable asset for producing intricate components, prototypes, and complex parts requiring high dimensional accuracy.4. Company's commitment to innovation:With its groundbreaking 4-axis lathe, the manufacturer continues its tradition of pushing the boundaries of machining technology. Known for its dedication to research and development, the company has aimed to deliver advanced solutions that adapt to the evolving needs of the industry. By incorporating the latest innovations into their machinery, they consistently offer state-of-the-art products that boost productivity, reduce costs, and maximize operational efficiency for their clients.Conclusion:As the machinery industry continues to evolve, the introduction of the advanced 4-axis lathe by this leading manufacturer marks a significant milestone. This cutting-edge lathe is set to redefine machining capabilities by offering enhanced precision, increased productivity, and superior machining quality. With its versatile features and user-friendly operation, this 4-axis lathe is poised to become an indispensable tool for various industries, catering to their diverse machining needs. The manufacturer's commitment to innovation reinforces their position as an industry leader, consistently delivering groundbreaking solutions to propel the machining sector into the future.
Unlocking the Potential of Insert Moulding: Explore its Benefits and Applications
[News Headline]Innovative Insert Moulding Technology Enhances Efficiency and Durability in Manufacturing Processes[Subheading]Leading Manufacturing Company Unveils Remarkable Insert Moulding Technique That Revolutionizes the Industry[City, Date] - In a bid to revolutionize manufacturing processes, a renowned manufacturing company introduces an innovative insert moulding technology that enhances efficiency, durability, and cost-effectiveness. This groundbreaking technique aims to address long-standing challenges faced by various industries and is set to provide a significant boost to the manufacturing sector.[City, Date] - With the rapid advancement of technology, manufacturers strive to stay ahead of the curve by implementing cutting-edge techniques and technologies. With the rise in customer demand for improved efficiency, increased durability, and cost-effectiveness, companies such as [Company Name] have answered the call with their groundbreaking insert moulding technology.Insert moulding, also known as overmoulding, is a highly specialized manufacturing process that involves injecting a pre-formed component, such as metal, plastic, or electronic parts, into a plastic mould. This innovative technique provides multiple advantages over traditional manufacturing methods, making it an attractive option for a wide range of industries.One significant advantage of insert moulding is the enhanced durability it offers. The process ensures that the inserted component is securely encased within the plastic material, providing added protection from external forces, reducing the risk of damage and increasing the lifespan of the final product. This durability is particularly beneficial in industries that require high-performance components, such as the automotive, aerospace, and electronics sectors.Moreover, insert moulding significantly streamlines the manufacturing process. By combining multiple manufacturing steps into one, companies can save time and resources, ultimately reducing production costs. This streamlined approach also reduces the potential for errors and inconsistencies commonly associated with manual assembly, ensuring a more precise and uniform final product.With the advent of insert moulding, manufacturers can also explore more intricate and complex designs. This technique allows for the creation of parts with intricate geometries and multiple materials, expanding the possibilities for innovative product design. Additionally, insert moulding enables designers to incorporate multiple functionalities into a single component, further enhancing efficiency and overall product performance.Speaking at a recent press conference, [Company Name]'s spokesperson highlighted the benefits of their insert moulding technology. "As a leader in the manufacturing industry, we continually strive to push the boundaries of innovation. Our insert moulding technique offers unparalleled advantages, ranging from increased durability and efficiency to expanded design possibilities. We are excited to provide our clients with this cutting-edge solution that can unlock significant improvements in their manufacturing processes."The introduction of insert moulding into the manufacturing industry marks a pivotal stage in the evolution of production techniques. With the increasing demand for efficient, durable, and cost-effective products, companies must adapt and embrace innovative technologies such as insert moulding to remain competitive.As various industries adopt this remarkable technology, it is expected to revolutionize production processes across the board. From automotive and aerospace to electronics and medical sectors, insert moulding will undoubtedly drive efficiency and durability to new heights, benefiting manufacturers and end-users alike.In a rapidly changing world, the introduction of insert moulding technology demonstrates the ability of companies like [Company Name] to continually innovate and provide solutions that meet the evolving needs of the manufacturing industry. As the demand for enhanced efficiency and durability continues to grow, insert moulding proves to be a game-changer for businesses aiming to stay ahead in a highly competitive market.
Mastering the Art of Precision CNC Machining: Unveiling the Secrets to Perfect Metal Fabrication
Precision CNC Machining: Revolutionizing the Manufacturing IndustryIn today's fast-paced and technologically advanced world, businesses in diverse industries are constantly seeking ways to enhance their production processes. Efficiency, accuracy, and flexibility have become key parameters for success in the manufacturing sector. One such innovation that has gained immense popularity is precision CNC machining.Precision CNC machining is a cutting-edge manufacturing process that utilizes computer numerical control (CNC) systems to automate machine tools. This highly efficient method has revolutionized various industries by offering unmatched precision, reliability, and speed, thus increasing productivity and reducing costs.{Company introduction} has emerged as a leading player in the precision CNC machining market. With a rich history spanning several decades, the company has established a strong reputation for delivering high-quality products, exceptional customer service, and innovative solutions.The advent of precision CNC machining has significantly transformed the manufacturing landscape. By employing advanced software and hardware, CNC machines can accurately and efficiently shape a wide range of materials, including metals, plastics, and composites. From large-scale mass production to intricate custom-made parts, precision CNC machining enables businesses to create complex geometries with exceptional precision and repeatability.The benefits of precision CNC machining are manifold. Firstly, it eliminates the potential for human error, ensuring consistently accurate results. This aspect is critical for applications where precision and repeatability are paramount. Additionally, CNC machines can operate continuously, reducing downtime and enhancing productivity. This attribute enables manufacturers, including those in the automotive, aerospace, and medical sectors, to meet tight deadlines and fulfill increasing customer demands.The flexibility of CNC machines is another advantage that has driven their widespread adoption. These machines can quickly switch between various tools and adapt to diverse design specifications. In addition, the ability to modify designs through computer programming allows for rapid prototyping and iterative product development.Moreover, precision CNC machining offers notable cost savings in the long run. While the initial investment may be higher compared to conventional machining methods, the reduction in scrap, rework, and labor costs leads to significant overall savings. Furthermore, CNC machines can consistently produce high-quality parts, thereby minimizing the need for extensive quality control procedures.{Company} has been at the forefront of harnessing the power of precision CNC machining. With state-of-the-art facilities equipped with advanced CNC machines, the company offers a diverse range of machining services. Their team of highly skilled technicians and engineers ensures that every project meets the strictest quality standards and customer specifications. From rapid prototyping to high-volume production, {Company} has the expertise and capacity to cater to a wide array of customer requirements.The impact of precision CNC machining extends far beyond the manufacturing industry. It has also revolutionized sectors such as automotive, aerospace, electronics, and medical devices. Automotive companies, for instance, benefit from CNC machines that can precisely shape engine components and intricate interiors. Similarly, aerospace manufacturers rely on CNC machining for producing complex aircraft parts, such as turbine blades, with exceptional accuracy and strength.As the global manufacturing sector continues to evolve, precision CNC machining is expected to play an even more significant role. Rapid technological advancements, such as the integration of artificial intelligence and machine learning, are poised to further enhance the capabilities of CNC machines. These advancements will enable businesses to achieve unprecedented levels of efficiency, quality, and customization, giving them a competitive edge in the global marketplace.In conclusion, precision CNC machining has emerged as a game-changer in the manufacturing industry. {Company}, with its expertise and commitment to excellence, has cemented its position as a leader in this field. As industries continue to embrace this highly efficient and reliable method, precision CNC machining will undoubtedly reshape the way products are manufactured worldwide. The future of manufacturing has arrived, and it is powered by precision CNC machining.
How to Make a Prototype Mold Efficiently and Effectively
Title: Advancements in Prototype Mold Making Revolutionize Manufacturing ProcessesIntroduction:In recent decades, prototype mold making has become an integral part of product development for various industries, catering to the ever-increasing demand for accurate and efficient manufacturing processes. One company at the forefront of this innovative technology is a leading industry player whose expertise has revolutionized prototype mold making. Drawing upon years of experience and continually pushing the boundaries of what's possible, they are proving to be a game-changer in the manufacturing landscape.Streamlining the Manufacturing Process:Prototype mold making plays a crucial role in transforming conceptual designs into tangible products. It enables manufacturers to create prototypes with intricate details while simultaneously reducing lead times and costs. This advancement has resulted in an accelerated production process and allows companies the opportunity to swiftly bring new and innovative ideas to market.Advanced Design Capabilities:With a keen focus on cutting-edge technology, the company has introduced unique design capabilities that have revolutionized the prototype mold making process. By collaborating closely with their clients, they can accurately translate design concepts into highly functional molds, ensuring maximum precision and efficiency.Their team of skilled engineers employs innovative techniques and state-of-the-art equipment to create molds that meet exact specifications. By utilizing cutting-edge software, they are able to simulate the manufacturing process, identifying potential flaws and making necessary adjustments before production even begins. This approach significantly reduces rework time and helps bring products to the market faster.Precision Manufacturing:In the realm of prototype mold making, precision is key. With years of experience, the company prides itself on its ability to deliver molds with impeccable accuracy. Their team of highly skilled craftsmen utilizes modern tooling equipment to achieve intricate details and maintain consistently high quality.Furthermore, the company places a strong emphasis on quality assurance, utilizing stringent inspection methods to ensure that each mold meets the highest standards. Through rigorous testing and evaluation, they guarantee that the final product is flawless, eliminating costly production errors.Environmental Consciousness:Recognizing the need for environmentally friendly practices in the manufacturing industry, the company has embraced sustainable methods for prototype mold making. By utilizing recyclable materials and implementing energy-efficient processes, they are dedicated to reducing their carbon footprint and promoting a greener approach to manufacturing. Collaboration and Customer Satisfaction:The company prides itself on establishing collaborative partnerships with its clients, understanding that clear communication and open dialogue are essential to success. By working closely with customers during the entire prototype mold making process, they ensure that the final mold meets their exact specifications.Customer satisfaction is of paramount importance to the company, and they consistently strive to exceed expectations. With a commitment to delivering high-quality molds while adhering to strict timelines, they have garnered a reputation as a dependable and trusted manufacturing partner.Future Outlook:As the demand for innovative and efficient manufacturing processes continues to rise, prototype mold making stands as a critical link between design and production. The company's dedication to pushing the boundaries of what is possible in the field ensures that they will remain at the forefront of this industry for years to come.Conclusion:Through advancements in design capabilities, precision manufacturing, and a strong commitment to customer satisfaction, the company has transformed prototype mold making into an essential component of the manufacturing process. By utilizing innovative technology, they have revolutionized the industry, bringing products from concept to production faster and more efficiently than ever before. With a forward-thinking approach and a dedication to quality, they have cemented their position as a leader in prototype mold making.
Mastering the Art of Precision Lathe Turning: Latest News Insights Revealed
Precision Lathe Turning Technology Empowers Industries with Unparalleled Accuracy and Efficiency(Please note: The brand name has been removed from the title for neutrality)In the world of manufacturing, precision is everything. Companies across various industries strive to optimize their production processes to ensure the highest levels of accuracy and efficiency. One technology that has proven to be essential in achieving these goals is Precision Lathe Turning.Precision Lathe Turning is a machining technique that involves the use of a lathe machine to shape and refine materials with utmost accuracy. By rotating the material against a cutting tool, the lathe machine enables manufacturers to craft complex shapes, tight tolerances, and polished finishes. The versatility of this technology has made it indispensable across industries such as automotive, aerospace, electronics, and more.To gain a deeper understanding of Precision Lathe Turning, let's explore its benefits, applications, and how it has revolutionized manufacturing processes.Precision Lathe Turning offers immense advantages over traditional machining methods. Firstly, it enables manufacturers to achieve precise measurements with consistent accuracy. This means that components produced through Precision Lathe Turning can fit together flawlessly, reducing the risk of error and enhancing overall product quality. Additionally, the superior surface finish achieved by this technique eliminates the need for additional polishing or treatment processes, saving time, cost, and resources.Moreover, Precision Lathe Turning is highly efficient, allowing companies to meet tight production schedules without compromising quality. The ability to automate and program lathe machines ensures repetitive tasks are performed accurately and at high speeds. This, in turn, boosts overall productivity and reduces manufacturing lead times considerably.The applications of Precision Lathe Turning are diverse and far-reaching. In automotive manufacturing, this machining technique is used to create critical components such as pistons, crankshafts, and gears. By employing Precision Lathe Turning, manufacturers can ensure precise dimensions, proper balance, and smooth operation, thereby enhancing the overall performance and reliability of vehicles.In the aerospace industry, Precision Lathe Turning plays a crucial role in crafting intricate turbine components, propellers, and engine parts. The high level of dimensional accuracy achieved through this technology is paramount in ensuring optimal aerodynamic performance and safety in flight.Precision Lathe Turning is also extensively utilized in electronics manufacturing. From producing connectors and sockets to intricate parts for advanced electronic devices, manufacturers in this industry rely on the precision and efficiency provided by lathe machines. The ability to manufacture components with intricate designs, tight tolerances, and high-quality finishes is paramount in meeting the demands of the rapidly evolving electronics market.When it comes to Precision Lathe Turning, companies trust the expertise and reliability of leading precision machining providers. One such company, which has established itself as a pioneer in the field, offers exceptional Precision Lathe Turning services to cater to various industry needs. With state-of-the-art equipment and a highly skilled team, this company consistently delivers unparalleled accuracy, efficiency, and customer satisfaction."We strive to provide our clients with the highest quality Precision Lathe Turning services," says the company spokesperson. "Our commitment to utilizing cutting-edge technology, combined with the expertise of our technicians, allows us to meet the unique requirements of each industry we serve. Whether it's automotive, aerospace, electronics, or any other sector, we aim to empower our clients with precision solutions that enable them to thrive in an increasingly competitive market."In conclusion, Precision Lathe Turning has emerged as a game-changer in the manufacturing industry. Its ability to deliver unparalleled accuracy, efficiency, and versatility has made it an indispensable technology across various sectors. As industries continue to advance, manufacturers must embrace Precision Lathe Turning to remain competitive and stay at the forefront of technological innovation. By harnessing the power of this machining technique, companies can elevate their production processes to new heights, ensuring exceptional quality and customer satisfaction every step of the way.
Unlocking the Potential of Rapid Tooling Injection Molding for Advanced Manufacturing
Title: Advancements in Rapid Tooling Injection Molding Streamline Manufacturing ProcessesIntroduction:In recent years, the manufacturing industry has witnessed remarkable advancements in technology, with rapid tooling injection molding emerging as a cutting-edge technique. This process allows for the production of high-quality prototype parts, reducing lead times and costs significantly. One prominent player in this field, [Company Name], has taken a leap forward with their innovative solutions and expertise in this domain. This article aims to delve into the world of rapid tooling injection molding and shed light on how [Company Name] is revolutionizing manufacturing processes.Rapid Tooling Injection Molding:Rapid tooling injection molding, also known as RTIM, is a manufacturing technique that combines traditional injection molding methods with rapid prototyping technologies. This process involves the production of tooling inserts using additive manufacturing techniques or subtractive processes like CNC machining. These inserts are then integrated into injection molds, enabling the mass production of high-quality plastic parts in a short period.By significantly reducing lead times, RTIM allows manufacturers to bring products to market faster, giving them a competitive edge. Additionally, this technique eliminates the need for expensive and time-consuming metal tooling, making it an attractive option for small-scale production runs, prototypes, and low-volume manufacturing.[Company Name]'s Innovative Solutions:[Company Name] is a leading player in the field of rapid tooling injection molding. With their expertise and dedication to innovation, they have developed a range of solutions that have wide-ranging applications across industries.1. Advanced Material Selection:[Company Name] understands the importance of selecting the right materials for each project. They offer a wide variety of thermoplastics and specialty materials, ensuring the utmost precision, durability, and functional performance in the final product. By leveraging their materials expertise, they can cater to diverse customer requirements, from medical-grade parts to aerospace components.2. Design Optimization:One of the significant advantages of rapid tooling injection molding is the ability to optimize designs quickly. [Company Name] employs design engineers who work closely with clients to enhance the manufacturability of their products. By utilizing advanced simulation techniques, they identify potential design flaws early in the process, reducing iterations and achieving higher quality end products efficiently.3. Automation and Robotics:To further enhance efficiency, [Company Name] leverages automation and robotics in their manufacturing processes. This integration streamlines operations, reducing human error and enhancing overall production output. The company's investment in cutting-edge automation technology ensures consistent, high-quality parts while maintaining cost-effectiveness.4. Quality Control and Testing:[Company Name] places utmost importance on quality control and testing throughout the manufacturing process. By employing stringent quality assurance protocols, including dimensional analysis, functionality testing, and surface finish inspections, they ensure that the final products meet or exceed industry standards. This commitment to quality has earned them a solid reputation among their clientele.Conclusion:Rapid tooling injection molding has revolutionized the manufacturing industry by enabling fast, cost-effective production of high-quality plastic parts. [Company Name], with its expertise and innovative solutions, has emerged as a key player in this field. Their commitment to material selection, design optimization, strategic automation, and rigorous quality control makes them an industry leader capable of meeting diverse customer requirements. As technology continues to evolve, it is exciting to witness the transformative impact rapid tooling injection molding, along with companies like [Company Name], is having on the manufacturing industry.