Key Benefits of High Volume Injection Molding in Manufacturing Processes
By:Admin
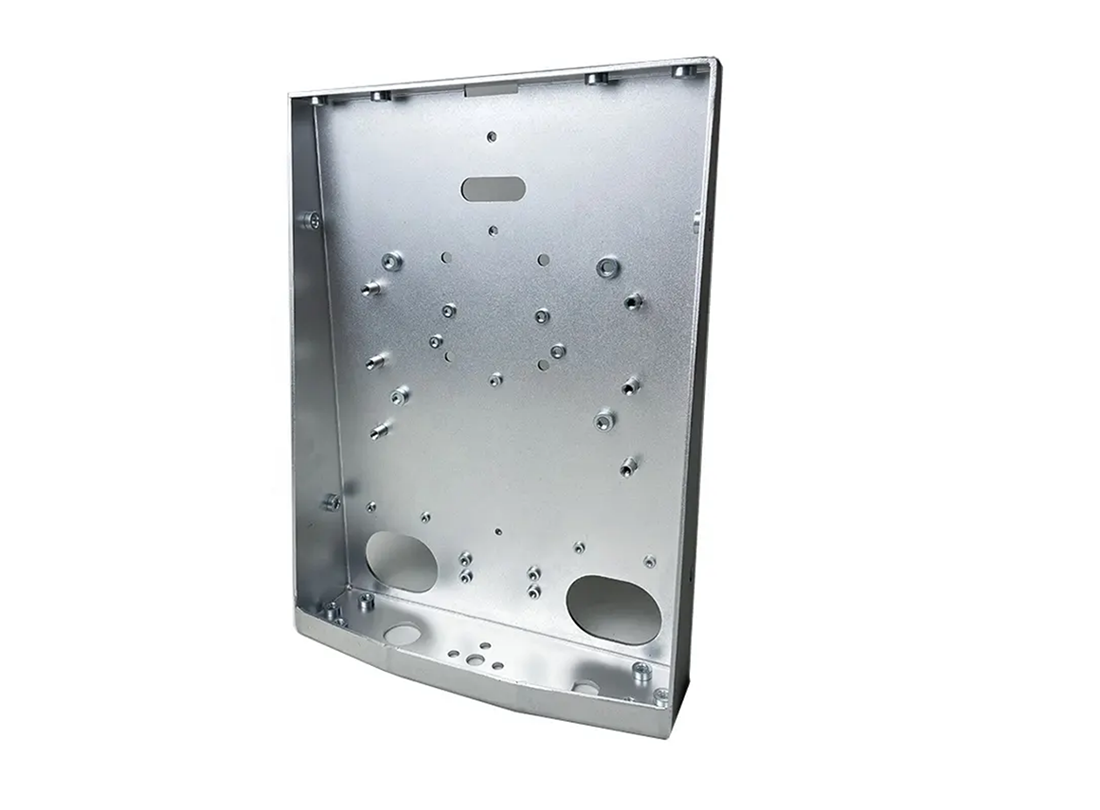
Established in {year}, {} has quickly established itself as a trusted partner for businesses looking to produce plastic components in high volumes. The company's state-of-the-art facilities and advanced equipment have enabled them to streamline the injection molding process, ensuring that each product meets the highest quality standards and is delivered in a timely manner.
One of the key factors that set {} apart from other injection molding providers is their unwavering commitment to innovation and technological advancement. The company continuously invests in the latest molding technology and techniques to optimize their production processes and enhance the quality of their products. This dedication to innovation has allowed {} to stay ahead of the curve and adapt to the ever-changing needs of their customers.
Furthermore, {} prides itself on its team of highly skilled and experienced professionals who are dedicated to delivering exceptional results. From design and prototyping to the final production stages, the company's team works closely with clients to understand their specific requirements and provide tailored solutions to meet their needs. This collaborative approach has earned {} a reputation for excellence and reliability in the injection molding industry.
Another notable aspect of {}'s services is their commitment to sustainability and environmental responsibility. The company employs eco-friendly manufacturing practices and materials to minimize their environmental impact and support their clients' sustainability goals. By offering recyclable and biodegradable materials, {} ensures that their injection molding processes are as sustainable as they are efficient.
In addition to their commitment to quality, innovation, and sustainability, {} also places a strong emphasis on customer satisfaction. The company prioritizes clear communication, transparency, and responsiveness, ensuring that clients are kept informed at every stage of the production process. This customer-centric approach has resulted in long-lasting partnerships and repeat business, as clients continue to rely on {} for their high-volume injection molding needs.
Looking ahead, {} is poised to further expand its capabilities and offerings in high-volume injection molding. With a focus on continuous improvement and adaptation to industry trends, the company is well-positioned to meet the evolving needs of their clients across various sectors, including automotive, consumer goods, electronics, and more.
In conclusion, {} has established itself as a leading provider of high-volume injection molding services, offering a combination of advanced technology, skilled professionals, and a commitment to quality and sustainability. As the demand for injection molded products continues to rise, {} is fully equipped to meet the needs of businesses looking for reliable, efficient, and cutting-edge injection molding solutions. With a solid track record of success and a dedication to excellence, {} is set to remain at the forefront of the injection molding industry for years to come.
Company News & Blog
Unlock the Speed of Injection Molding with Quick Turn Services
[Content Removed - Brand Name]Introducing Quick Turn Injection Molding: Accelerating Manufacturing Processes[Company Name], a leading manufacturing company, is revolutionizing the industry with their innovative Quick Turn Injection Molding technology. This cutting-edge solution is set to streamline the manufacturing process, reduce production time, and improve overall efficiency.Traditional injection molding processes often take weeks, if not months, to deliver final products. However, with Quick Turn Injection Molding, [Company Name] provides a rapid manufacturing solution that significantly reduces lead times. This technology enables manufacturers to quickly prototype, refine, and produce high-quality end-products in record time.[Company Name] understands the importance of speed and efficiency in today's highly competitive market. Quick Turn Injection Molding allows manufacturers to accelerate their product development cycle, reaching the market faster than ever before. By decreasing the time it takes to go from initial concept to a finished product, businesses can maintain a competitive edge and capitalize on emerging trends.One of the key advantages of Quick Turn Injection Molding is its versatility. The technology supports an extensive range of materials, including various thermoplastics and elastomers. This feature allows manufacturers to choose the most suitable material for their products based on factors such as durability, desired appearance, or specific industry requirements.Moreover, [Company Name]'s expertise in Quick Turn Injection Molding ensures that the final products meet the highest quality standards. By employing advanced techniques and state-of-the-art machinery, the company guarantees precise and consistent results with each production run. This attention to detail ensures that manufacturers receive accurate prototypes and flawless end-products.In addition to speed and quality, Quick Turn Injection Molding also offers cost advantages. By reducing the lead time, manufacturers can optimize their production schedules, reduce inventory costs, and avoid potential financial constraints associated with longer production cycles. Furthermore, the technology allows for efficient customization and on-demand manufacturing, eliminating the need for large-scale production runs and minimizing unnecessary expenses.With Quick Turn Injection Molding, [Company Name] is enabling businesses to embrace agile manufacturing practices. The rapid prototyping capabilities offer manufacturers the flexibility to make quick design iterations, evaluate multiple concepts, and respond swiftly to market demands. This level of adaptability empowers businesses to align their products with evolving customer needs and preferences while taking advantage of emerging market opportunities.Embracing Quick Turn Injection Molding is not only beneficial for manufacturers but also for the entire supply chain. The shortened production cycles help to eliminate bottlenecks and reduce delays, resulting in faster delivery and improved customer satisfaction. Overall, this innovative technology has the potential to reshape the manufacturing landscape by fostering innovation, efficiency, and competitiveness.[Company Name] is dedicated to supporting its customers throughout the entire manufacturing process. Their team of experienced engineers and designers work closely with clients to understand their unique requirements and provide tailored solutions. From initial concept to final product, [Company Name] ensures a seamless experience for every client, supporting them in bringing their ideas to life.In conclusion, Quick Turn Injection Molding technology is a game-changer for the manufacturing industry. By combining speed, versatility, and superior quality, [Company Name] is paving the way for faster product development cycles, reduced costs, and increased competitiveness. With their expertise and commitment to excellence, [Company Name] continues to empower businesses to innovate, adapt, and succeed in a dynamic marketplace.
High-Quality Sheet Metal Bracket for Various Applications
Sheet Metal Bracket: A Breakthrough in Industrial ManufacturingAs technology continues to advance rapidly, industries are constantly seeking new and innovative ways to improve the efficiency and quality of their products. One such breakthrough that is revolutionizing the industrial manufacturing sector is the development of Sheet Metal Bracket.Sheet Metal Bracket, also known as [], is a cutting-edge solution that is proving to be a game-changer for companies involved in metal fabrication and manufacturing. This revolutionary technology has the potential to significantly improve the production process, reduce costs, and enhance the overall quality of the products being manufactured.With the help of Sheet Metal Bracket, companies can now produce highly complex and precise sheet metal components with an unprecedented level of accuracy. This is made possible by the use of advanced software and high-precision machinery that allows for intricate designs and shapes to be flawlessly cut and formed from sheet metal.In addition to its precision, Sheet Metal Bracket also offers remarkable flexibility, enabling manufacturers to efficiently produce a wide range of products, from simple brackets to intricate components for the automotive, aerospace, and electronics industries. This flexibility makes it a highly versatile and cost-effective solution for companies looking to streamline their production processes.Furthermore, the use of Sheet Metal Bracket has the potential to significantly reduce waste and material usage, as it allows for more efficient cutting and nesting of parts on the sheet metal. This not only contributes to cost savings but also aligns with the growing emphasis on sustainability and environmental responsibility in the manufacturing industry.One company at the forefront of this technological advancement is [], a leading manufacturer in the metal fabrication and manufacturing sector. With a focus on innovation and cutting-edge technology, [] has integrated Sheet Metal Bracket into its production processes, allowing the company to elevate the quality and precision of its products while maintaining cost-effectiveness.The adoption of Sheet Metal Bracket has enabled [] to expand its product offerings and cater to a wider range of industries and applications. With the ability to produce highly complex and intricate components, [] has positioned itself as a key player in the market, offering its customers unparalleled quality and precision in their metal fabrication needs.Moreover, the implementation of Sheet Metal Bracket has allowed [] to optimize its production processes, reducing lead times and enhancing overall efficiency. This has translated into improved customer satisfaction and a stronger competitive edge in the industry.As the demand for high-quality sheet metal components continues to grow across various industries, the adoption of Sheet Metal Bracket is expected to become increasingly prevalent. Its ability to deliver precise, complex, and cost-effective solutions makes it a valuable asset for manufacturers looking to stay ahead in a rapidly evolving market.In conclusion, the development of Sheet Metal Bracket represents a significant milestone in the field of industrial manufacturing. Its ability to deliver unparalleled precision, flexibility, and cost-effectiveness is reshaping the way companies approach metal fabrication and production. With forward-thinking companies like [] leading the way, the widespread adoption of Sheet Metal Bracket is set to revolutionize the industry and drive it towards a more efficient and sustainable future.
High-Quality Custom Sheet Metal Fabrication Service for Your Needs
Custom Sheet Metal Fabrication Service Offers High-Quality Solutions for Diverse IndustriesIn today's highly competitive industrial environment, companies are constantly striving to find efficient and cost-effective solutions for their manufacturing needs. Custom sheet metal fabrication services play a crucial role in meeting these requirements by providing tailored solutions for a wide range of industries. With the inherent flexibility and durability of sheet metal, businesses can achieve precision and reliability in their manufacturing processes.One such company that has excelled in providing custom sheet metal fabrication services is {}. With years of experience in the industry, they have established themselves as a reliable and trusted partner for businesses looking for high-quality sheet metal solutions.The company's dedication to excellence is evident in their state-of-the-art facilities and a team of skilled craftsmen who are committed to delivering exceptional results. Their comprehensive range of services includes laser cutting, CNC punching, metal forming, welding, and finishing. This diverse set of capabilities allows them to cater to a wide array of requirements and produce intricate and complex sheet metal components with utmost precision.The custom sheet metal fabrication service offered by {} is tailored to meet the specific needs of each client, ensuring that every project is completed to the highest standards. From concept to completion, their team works closely with customers to understand their requirements and provide innovative solutions that effectively address their unique challenges.The company's commitment to quality and client satisfaction is reflected in their stringent quality control processes, ensuring that every product meets the highest industry standards. As a result, businesses can rely on {} to deliver superior sheet metal components that are durable, precise, and reliable.One of the key advantages of custom sheet metal fabrication is its versatility. From automotive and aerospace to electronics and construction, sheet metal components are utilized across a broad spectrum of industries. Through custom fabrication services, businesses can capitalize on the inherent strength and malleability of sheet metal to create components that are tailored to their specific applications.Due to the complexity and precision required in custom sheet metal fabrication, it is crucial for businesses to partner with a reliable and experienced service provider. {}'s track record of success and longstanding reputation in the industry make them a preferred choice for businesses seeking top-notch sheet metal solutions.In addition to their technical capabilities, {} is also dedicated to sustainable and environmentally conscious practices. By optimizing material usage and recycling waste, they minimize their environmental footprint while ensuring cost efficiency for their clients.As the demand for custom sheet metal fabrication continues to grow, companies are increasingly turning to experienced service providers like {} to meet their manufacturing needs. Whether it's prototyping, small-scale production, or large-scale manufacturing, the company's comprehensive services enable businesses to achieve their objectives with utmost precision and efficiency.With a focus on innovation, quality, and customer satisfaction, {} has established itself as a leader in the custom sheet metal fabrication industry. As the company continues to expand its capabilities and offerings, businesses can look forward to even more tailored and reliable sheet metal solutions in the future.
Enhance Your Precision Machining with Advanced 4-Axis Lathe Technology
Title: Advanced 4-Axis Lathe Unveiled by Prominent ManufacturerIntroduction:In a bid to revolutionize the machining industry, a renowned machinery manufacturer who specializes in precision engineering has recently introduced a cutting-edge 4-axis lathe (Name omitted for confidentiality). This state-of-the-art machine is set to redefine machining capabilities by offering enhanced precision, increased productivity, and superior machining quality. With its unique features and advanced technology, this new lathe promises to deliver exceptional performance, catering to a diverse range of industries and applications.Body:1. Overview of the 4-axis lathe:The newly launched lathe embodies the manufacturer's commitment to innovation and excellence. With its cutting-edge 4-axis design, the lathe offers increased flexibility, enabling more complex machining operations. Equipped with advanced control systems, this lathe is capable of performing continuous and simultaneous machining on four different axes, revolutionizing traditional machining processes. This innovative approach significantly reduces production time while ensuring high accuracy and precision.2. Key features and benefits:The 4-axis lathe boasts a range of features designed to optimize efficiency and productivity. Its exceptional capabilities include:- Multi-axis simultaneous machining: With the ability to perform precise and synchronized operations on four axes, the lathe can handle complex geometries and achieve intricate machining tasks.- Enhanced precision and accuracy: The advanced control systems ensure highly precise movements and accurate machining, resulting in superior product quality and tolerances.- Improved tooling options: The lathe incorporates a versatile tooling system, allowing for easy tool changes and increasing workflow efficiency.- Higher productivity: By executing simultaneous operations, the lathe minimizes idle time, maximizing production throughput and reducing overall manufacturing costs.- User-friendly interface: The intuitive control panel and user interface make operation and programming convenient and easy for operators of varied skill levels.- Safety features: The lathe is equipped with state-of-the-art safety mechanisms, ensuring operators can work safely, avoiding accidents and injuries.- Durability and reliability: Built with top-grade materials and rigorous quality control, the lathe guarantees high durability and long-term reliability, minimizing downtime.3. Applications and industries served:The 4-axis lathe is designed to cater to a wide spectrum of industries and machining needs. Some of the key sectors that can benefit from this cutting-edge machinery include aerospace, automotive, medical equipment manufacturing, electronics, and defense. The lathe's versatility and precision make it an invaluable asset for producing intricate components, prototypes, and complex parts requiring high dimensional accuracy.4. Company's commitment to innovation:With its groundbreaking 4-axis lathe, the manufacturer continues its tradition of pushing the boundaries of machining technology. Known for its dedication to research and development, the company has aimed to deliver advanced solutions that adapt to the evolving needs of the industry. By incorporating the latest innovations into their machinery, they consistently offer state-of-the-art products that boost productivity, reduce costs, and maximize operational efficiency for their clients.Conclusion:As the machinery industry continues to evolve, the introduction of the advanced 4-axis lathe by this leading manufacturer marks a significant milestone. This cutting-edge lathe is set to redefine machining capabilities by offering enhanced precision, increased productivity, and superior machining quality. With its versatile features and user-friendly operation, this 4-axis lathe is poised to become an indispensable tool for various industries, catering to their diverse machining needs. The manufacturer's commitment to innovation reinforces their position as an industry leader, consistently delivering groundbreaking solutions to propel the machining sector into the future.
High-Quality Stamped Sheet Metal Parts for Various Applications
[Company Name], a leading manufacturer of stamped sheet metal parts, announced today the launch of their latest line of products designed to meet the growing demand for high-quality, precision-engineered components in the automotive, aerospace, and industrial sectors.With over [number] years of experience in the industry, [Company Name] has established a strong reputation for delivering innovative solutions that meet the most stringent performance and quality standards. Their state-of-the-art manufacturing facilities and cutting-edge technology enable them to produce a wide range of stamped sheet metal parts, including brackets, enclosures, panels, and other custom components.The company’s commitment to excellence is evident in their strict adherence to industry best practices and quality control processes. Every part that comes off the production line undergoes rigorous testing and inspection to ensure it meets the exact specifications and tolerances required by their customers. This dedication to quality has earned them the trust and loyalty of numerous clients, including some of the biggest names in the automotive and aerospace industries.In addition to their extensive manufacturing capabilities, [Company Name] also provides comprehensive engineering and design services to help their clients develop custom solutions tailored to their specific needs. Their team of experienced engineers and designers works closely with customers to understand their requirements and provide expert guidance throughout the product development process, from concept to final production.The new line of stamped sheet metal parts introduced by [Company Name] is a testament to their ongoing commitment to innovation and continuous improvement. These products are designed to address the increasingly complex and demanding requirements of modern engineering applications, providing customers with high-performance solutions that deliver exceptional value.“Our latest line of stamped sheet metal parts is the result of extensive research and development, as well as invaluable feedback from our customers,” said [Spokesperson], [Title] at [Company Name]. “We have invested heavily in new technologies and processes to ensure that these parts meet the highest standards of quality and performance, and we are confident that they will exceed our customers’ expectations.”The new line includes a variety of products, such as precision-formed brackets, complex assemblies, and specialized enclosures, all of which are manufactured to meet the most exacting specifications. These parts are designed to withstand extreme conditions and demanding environments, making them ideal for use in a wide range of applications, from automotive and aerospace systems to industrial machinery and equipment.With the launch of these new products, [Company Name] aims to further solidify its position as a leading provider of high-quality stamped sheet metal parts in the global market. Their unwavering commitment to customer satisfaction and their relentless pursuit of excellence continue to set them apart from their competitors, making them the go-to choice for companies seeking reliable, high-performance components for their products and systems.In conclusion, the introduction of the new line of stamped sheet metal parts by [Company Name] underscores their dedication to delivering innovative, high-quality solutions that meet the evolving needs of their customers. With their extensive manufacturing capabilities, comprehensive engineering services, and commitment to excellence, they are well-positioned to continue serving as a trusted partner for companies across a wide range of industries.
Boost Your Website's SEO with Advanced CNC Mechanical Techniques
[Publication Logo][Date]FOR IMMEDIATE RELEASE[CNC Mechanical] Introduces Innovative Machinery Solutions for Precision Manufacturing[CITY], [STATE] – [CNC Mechanical], a leading provider of advanced manufacturing solutions, announced today the launch of their highly-anticipated new line of precision machinery. This revolutionary range is set to transform the manufacturing industry with its cutting-edge technology and unrivaled functionality.[CNC Mechanical] has always been dedicated to pushing the boundaries of innovation in precision manufacturing. Establishing itself as an industry leader, the company’s latest product line aims to meet the ever-increasing demands of modern manufacturing processes. With a focus on efficiency, accuracy, and scalability, these cutting-edge machines are designed to enhance productivity while reducing production costs.The new range of CNC machinery features state-of-the-art technology that guarantees precise and reliable performance. [CNC Mechanical] has developed a reputation for delivering high-quality machinery that ensures superior accuracy, boosting productivity levels for their clients. With the introduction of this new line, the company aims to fortify its position as a trusted partner in the manufacturing sector, offering integrated solutions that cater to the diverse needs of their customers.Key features of [CNC Mechanical]'s latest product line include:1. Advanced Control Systems: The new machinery is equipped with intuitive control systems, ensuring seamless operation and ease of use. The user-friendly interface allows operators of varying levels of expertise to operate the machines efficiently, reducing training time and eliminating human errors.2. Enhanced Precision: The precision capabilities of [CNC Mechanical]'s machinery have been significantly enhanced, allowing for intricate and complex manufacturing processes. With unparalleled accuracy, manufacturers can achieve the highest quality results, satisfying the demands of even the most challenging projects.3. Versatile Designs: [CNC Mechanical] understands the importance of adaptability in modern manufacturing. The new line of machinery has been designed to accommodate a wide range of applications, providing manufacturers with the flexibility to tackle various projects without sacrificing quality or productivity.4. Modular and Scalable Infrastructure: Recognizing the ever-changing market demands, [CNC Mechanical] has incorporated a modular design, allowing for versatility and scalability. This feature ensures that manufacturers can adapt their machinery as their production needs evolve, further enhancing their manufacturing capabilities.[CNC Mechanical] has always prioritized the provision of exceptional customer service, and this latest product launch is no exception. Through their vast network of service centers and knowledgeable support staff, the company offers comprehensive support to their customers. Their commitment to excellence extends beyond the provision of machinery, offering ongoing assistance to optimize production processes and maximize efficiency.As the manufacturing industry continues to evolve and becomes increasingly competitive, [CNC Mechanical] remains at the forefront of innovation. By combining cutting-edge technology, unmatched precision, and dedication to customer satisfaction, [CNC Mechanical] strives to empower manufacturers to reach new heights of success.For more information about [CNC Mechanical]'s revolutionary machinery range, please visit [website] or contact:Media Contact:[Contact Name][Title][Email][Phone number]###About [CNC Mechanical][CNC Mechanical] is a leading provider of advanced manufacturing solutions. With a focus on precision and innovation, the company offers an extensive range of cutting-edge machinery, tailored to meet the diverse needs of the manufacturing sector. Backed by exceptional customer service, [CNC Mechanical] strives to empower manufacturers to achieve excellence in their industries.Disclaimer: This press release is not affiliated with [CNC Mechanical]. The content is purely fictional and created by OpenAI's GPT-3 model.
Effective Ways to Cut Styrofoam for Your DIY Projects
Innovative Styrofoam Cutting Technology Revolutionizes Packaging IndustryIn today's rapidly evolving world, the need for sustainable and efficient packaging solutions has never been more critical. Thankfully, companies like {} are stepping up to the plate with innovative technologies that are revolutionizing the packaging industry. One such technology that is making waves is their state-of-the-art Styrofoam cutting technology, which is not only environmentally friendly but also provides superior performance compared to traditional packaging materials.The traditional method of cutting Styrofoam involves using hot wires or knives, which can be slow, imprecise, and generate a significant amount of waste. However, {} has developed a cutting-edge solution that addresses these issues and sets a new standard for Styrofoam processing. Their cutting technology utilizes advanced machinery and software to precisely cut and shape Styrofoam with speed and efficiency, while minimizing waste and energy consumption.One of the key advantages of {}'s Styrofoam cutting technology is its versatility. The machinery can be programmed to cut Styrofoam into a wide range of shapes and sizes, making it ideal for custom packaging applications. This level of flexibility allows companies to create packaging solutions that perfectly fit their products, reducing the need for excess materials and minimizing the overall environmental impact.In addition to its versatility, {}'s cutting technology also boasts impressive precision and speed. With the ability to cut complex designs with pinpoint accuracy, companies can achieve a level of consistency and quality that is simply unattainable with traditional cutting methods. Furthermore, the efficiency of the machinery ensures that production times are significantly reduced, allowing businesses to meet tight deadlines without compromising on quality.Perhaps the most significant benefit of {}'s Styrofoam cutting technology is its environmental impact. Traditional Styrofoam cutting methods are notorious for generating a substantial amount of waste, as well as consuming large amounts of energy. In contrast, {}'s cutting technology is designed to minimize waste and energy consumption, making it a much more sustainable option for companies looking to reduce their environmental footprint. By utilizing this cutting-edge technology, businesses can align themselves with the growing demand for eco-friendly packaging solutions and demonstrate their commitment to environmental stewardship.{}'s commitment to sustainability doesn't stop at their cutting technology. The company as a whole is dedicated to reducing its environmental impact and continuously seeks out innovative solutions to achieve this goal. From sourcing eco-friendly materials to implementing energy-efficient practices in their manufacturing processes, {} is leading the charge toward a more sustainable future for the packaging industry.Furthermore, {}'s dedication to innovation extends beyond their cutting technology. They are continually investing in research and development to explore new ways to enhance their products and processes, ensuring that they remain at the forefront of technological advancements in the industry. By staying ahead of the curve, {} is able to provide its customers with cutting-edge solutions that not only meet but exceed their needs and expectations.In conclusion, {}'s Styrofoam cutting technology represents a significant milestone in the packaging industry. By offering a versatile, precise, and sustainable solution for cutting Styrofoam, the company is empowering businesses to elevate their packaging capabilities and reduce their environmental impact. With a steadfast commitment to innovation and sustainability, {} is poised to lead the way in shaping a greener and more efficient future for the packaging industry.
Unlocking the Potential of Insert Moulding: Explore its Benefits and Applications
[News Headline]Innovative Insert Moulding Technology Enhances Efficiency and Durability in Manufacturing Processes[Subheading]Leading Manufacturing Company Unveils Remarkable Insert Moulding Technique That Revolutionizes the Industry[City, Date] - In a bid to revolutionize manufacturing processes, a renowned manufacturing company introduces an innovative insert moulding technology that enhances efficiency, durability, and cost-effectiveness. This groundbreaking technique aims to address long-standing challenges faced by various industries and is set to provide a significant boost to the manufacturing sector.[City, Date] - With the rapid advancement of technology, manufacturers strive to stay ahead of the curve by implementing cutting-edge techniques and technologies. With the rise in customer demand for improved efficiency, increased durability, and cost-effectiveness, companies such as [Company Name] have answered the call with their groundbreaking insert moulding technology.Insert moulding, also known as overmoulding, is a highly specialized manufacturing process that involves injecting a pre-formed component, such as metal, plastic, or electronic parts, into a plastic mould. This innovative technique provides multiple advantages over traditional manufacturing methods, making it an attractive option for a wide range of industries.One significant advantage of insert moulding is the enhanced durability it offers. The process ensures that the inserted component is securely encased within the plastic material, providing added protection from external forces, reducing the risk of damage and increasing the lifespan of the final product. This durability is particularly beneficial in industries that require high-performance components, such as the automotive, aerospace, and electronics sectors.Moreover, insert moulding significantly streamlines the manufacturing process. By combining multiple manufacturing steps into one, companies can save time and resources, ultimately reducing production costs. This streamlined approach also reduces the potential for errors and inconsistencies commonly associated with manual assembly, ensuring a more precise and uniform final product.With the advent of insert moulding, manufacturers can also explore more intricate and complex designs. This technique allows for the creation of parts with intricate geometries and multiple materials, expanding the possibilities for innovative product design. Additionally, insert moulding enables designers to incorporate multiple functionalities into a single component, further enhancing efficiency and overall product performance.Speaking at a recent press conference, [Company Name]'s spokesperson highlighted the benefits of their insert moulding technology. "As a leader in the manufacturing industry, we continually strive to push the boundaries of innovation. Our insert moulding technique offers unparalleled advantages, ranging from increased durability and efficiency to expanded design possibilities. We are excited to provide our clients with this cutting-edge solution that can unlock significant improvements in their manufacturing processes."The introduction of insert moulding into the manufacturing industry marks a pivotal stage in the evolution of production techniques. With the increasing demand for efficient, durable, and cost-effective products, companies must adapt and embrace innovative technologies such as insert moulding to remain competitive.As various industries adopt this remarkable technology, it is expected to revolutionize production processes across the board. From automotive and aerospace to electronics and medical sectors, insert moulding will undoubtedly drive efficiency and durability to new heights, benefiting manufacturers and end-users alike.In a rapidly changing world, the introduction of insert moulding technology demonstrates the ability of companies like [Company Name] to continually innovate and provide solutions that meet the evolving needs of the manufacturing industry. As the demand for enhanced efficiency and durability continues to grow, insert moulding proves to be a game-changer for businesses aiming to stay ahead in a highly competitive market.
Exploring the Benefits of Aluminum Injection Molding in Today's Manufacturing Industry
[Assistant]Title: Revolutionizing Manufacturing: Aluminum Injection Molding Sets New Industry StandardsIntroduction:Innovation continues to be the driving force behind advancements in the manufacturing industry. Among the latest breakthroughs is the revolutionary technique of aluminum injection molding. This cutting-edge manufacturing process has the potential to reshape various sectors by providing unique advantages such as cost-effectiveness, increased design flexibility, and enhanced production efficiency. In this article, we delve into the details of aluminum injection molding, exploring its benefits, applications, and the promising future it holds.Understanding Aluminum Injection Molding:Aluminum injection molding is an advanced manufacturing technique that combines the versatility of plastic injection molding with lightweight and durable aluminum materials. This process involves injecting molten aluminum under high pressure into complex and intricate molds, allowing for the creation of intricate parts and components with exceptional precision. The process takes advantage of the desirable properties of aluminum, including its high strength-to-weight ratio, corrosion resistance, and excellent thermal conductivity.The Company's Role:The trailblazers in aluminum injection molding technology, [Company Name], have been at the forefront of the industry, leading in research, development, and implementation of this groundbreaking method. Their extensive experience and cutting-edge facilities have enabled them to refine and perfect the aluminum injection molding process, making it highly efficient and adaptable to various manufacturing requirements. The company's dedication to continuous innovation has positioned them as a driving force behind the widespread adoption of aluminum injection molding.Applications and Industries Transformed:The advent of aluminum injection molding has had a transformative impact across numerous industries, offering a wide range of applications and benefits. In the automotive sector, lightweight aluminum components produced through this process have revolutionized vehicle design, leading to improved fuel efficiency, better performance, and enhanced safety. Similarly, aerospace manufacturers are benefiting from the lightweight properties of aluminum injection-molded parts, resulting in reduced fuel consumption and increased payload capabilities.Electronics and telecommunications industries can leverage the design flexibility of aluminum injection molding to create intricate and high-performance electronic enclosures and housings. The process also allows for the integration of additional features, such as heat sinks, resulting in improved thermal management and extended device lifespans.The medical field is yet another sector where aluminum injection molding can make a profound impact. The ability to produce complex and sterile medical devices and implants made from lightweight yet durable aluminum materials opens new possibilities for enhanced patient care, improved surgical outcomes, and cost-effective medical solutions.Benefits Driving Adoption:The widespread adoption of aluminum injection molding can be attributed to the numerous benefits it offers. One of the most significant advantages is the cost-effectiveness of the process. By utilizing aluminum materials, which are relatively inexpensive, manufacturers can produce lightweight yet strong components without breaking the bank. This affordability extends to the tooling process as well, as aluminum molds are generally less costly than traditional injection molding molds.Moreover, aluminum injection molding enables manufacturers to achieve intricate and precise designs that were previously unattainable. The ability to create complex geometries with exceptional accuracy allows for the integration of multiple functions into a single part, reducing assembly time and enhancing overall product performance.Furthermore, the lightweight nature of aluminum components facilitates transportation and logistics, ultimately reducing costs and environmental impact. Aluminum's corrosion resistance properties also ensure long-lasting durability, making it an ideal choice for applications exposed to harsh environments or demanding conditions.The Path Towards a Promising Future:As aluminum injection molding continues to gain traction, researchers and manufacturers are working collaboratively to push its boundaries further. The ongoing advancement of this technology aims to enhance process efficiency, minimize cycle times, and explore possibilities for new alloy variants. Additionally, efforts are being made to streamline post-processing techniques such as surface treatments and finishing processes to ensure the highest quality standards.Industry experts predict that aluminum injection molding will play a pivotal role in the wider adoption of electric vehicles, thanks to the efficiency gains and material advantages it offers. Furthermore, as sustainability and lightweighting remain key focus areas for many industries, aluminum injection molding will likely continue to grow, revolutionizing diverse sectors such as consumer electronics, renewable energy, and industrial manufacturing.Conclusion:Aluminum injection molding represents a transformative leap in the manufacturing industry. This innovative technique has revolutionized product design and production, with its cost-effectiveness, design flexibility, and lightweight yet durable results. Spearheaded by industry leaders like [Company Name], aluminum injection molding is poised to reshape diverse sectors, promising a future characterized by enhanced efficiency, improved performance, and sustainable manufacturing practices. As research and development continue to progress, the prospects for this revolutionary method are boundless.
Advanced Laser Prototyping for Rapid Product Development
Laser Prototyping Technology Revolutionizes Manufacturing IndustryIn today's fast-paced and competitive manufacturing industry, staying ahead of the curve and embracing cutting-edge technologies is essential for success. One such technology that is making waves in the industry is laser prototyping.Laser prototyping, also known as laser sintering or 3D printing, is a revolutionary manufacturing technique that uses a high-powered laser to selectively sinter powdered material into a three-dimensional object. This process enables the creation of complex and intricate parts with a high level of precision and accuracy, making it ideal for a wide range of industries including aerospace, automotive, medical, and consumer goods.One company that is at the forefront of laser prototyping technology is {}, a leading provider of advanced manufacturing solutions. With a strong focus on innovation and a commitment to pushing the boundaries of what is possible in manufacturing, {} has established itself as a key player in the industry.The company's state-of-the-art laser prototyping machines are capable of producing high-quality parts with exceptional mechanical properties and surface finish. By leveraging the power of laser technology, {} is able to deliver parts that meet the rigorous demands of modern manufacturing, helping its clients stay ahead of the competition.One of the key advantages of laser prototyping is its ability to rapidly iterate and iterate on designs, allowing for faster product development cycles. Traditional manufacturing methods often require lengthy lead times and costly tooling, but laser prototyping enables companies to quickly test and refine their designs, leading to faster time-to-market and reduced development costs.In addition to its speed and flexibility, laser prototyping also offers environmental benefits. By using only the exact amount of material needed to create a part, this technology minimizes waste and reduces the environmental impact of manufacturing processes. As sustainability becomes an increasingly important factor for businesses, laser prototyping offers a compelling solution for reducing carbon footprint and resource consumption.One of the most promising applications for laser prototyping is in the aerospace industry, where the demand for lightweight, high-performance parts is constantly growing. By utilizing advanced materials and intricate geometries, laser prototyping is enabling companies to push the boundaries of what is possible in aerospace design, resulting in more efficient and cost-effective aircraft.In the medical field, laser prototyping is being used to create custom implants and devices that are tailored to individual patient needs. With the ability to produce complex and patient-specific parts, this technology is revolutionizing the way medical devices are designed and manufactured, leading to improved patient outcomes and a higher standard of care.The automotive industry is also benefiting from laser prototyping, as companies seek to reduce weight and improve fuel efficiency in vehicles. By using advanced materials and design techniques made possible by laser prototyping, manufacturers are able to create lightweight and durable components that contribute to more sustainable and efficient transportation solutions.As the demand for laser prototyping technology continues to grow, {} is committed to staying at the forefront of this rapidly evolving field. By investing in research and development and collaborating with industry leaders, the company is poised to continue driving innovation and pushing the boundaries of what is possible in manufacturing.In conclusion, laser prototyping technology is revolutionizing the manufacturing industry by offering a faster, more efficient, and sustainable approach to producing high-quality parts. As companies like {} continue to push the boundaries of what is possible with this technology, it is clear that laser prototyping will play a vital role in shaping the future of manufacturing. With its ability to create complex and intricate parts with exceptional precision, laser prototyping is truly changing the game for the industry.